Heavy Duty Roller Chain Belt Conveyors
Conveying The World's Heaviest Recycling Materials Like MSW, Scrap Metal, Single Stream, Tissue, News Paper, Cardboard, Plastics, Aluminum, Shredded Material & More!
Roller Chain Conveyor Series Overview
Fluent RC Series of Conveyors are engineered with industry leading 3D CAD software and manufactured with precision (tolerances and standards). This series comes in standard and custom widths and lengths. Standard roller chain conveyor widths include 36″, 48″ 60”, 72″, 84”, 96”, 108” & 120”. Lower Horizontal lengths come in standard sizes of 10 feet, 15 feet 20 feet, 25 feet and 30 feet as well as any custom lower horizontal length to best match project specifications. The incline angles range from 25 degrees to 35 degrees depending on the application, material, baler requirements and building specifications. The standard chain sizes include 3 inch rollers with a 6 or 9 inch pitch, 4 & 5 inch roller with a 9 inch pitch. The frame is made of 3/16″ steel rectangular tubing, 1/4″ steel pan side walls, 1/4” steel rectangular tubing for supports & 25# – 30# rail track for chain support. The RC Series is MIG welded with certified welders and validated with a seamless QA process for overall structural integrity.
The Fluent RC Conveyors are sand blasted prior to paint, connected with grade 8 hardware (resist corrosion and increase strength), assembled and test run for over 10 hours prior to shipping. This series features industry leading components which include: rubber combo belts, apron pan belts, double beaded apron pan, z pan belts, hinged steel belts, motors, flame cut & hardened sprockets, electric oilers, coped angled cleats (2″, 3″, 4″ & 5″), side guards, bottom guards, e-stops, direct shaft mounted drives, cold rolled shafts and more.
This heavy duty series of conveyor is engineered and manufactured for the most extreme applications: wet, dry, high temps, e-waste, OCC, ONP, MSW, single stream, C&D, mining, biofuel, scrap, tire, stover, bagasse and more.
* We offer custom roller chain conveyors to meet the specific requirements for a wide variety of specialized applications (metering conveyors, high impact loading conveyors, reversing conveyors, etc.).
**This series of conveyors is often found feeding shredders, granulators, pulpers, balers, conveyors and sort stations for industry leading manufactures like Vecoplan, SSI, Granu-Tech, Ameri-Shred, Hustler Conveyors, CP Manufacturing, BHS, Harris Equipment, International Baler Corporation, American Baler, Excel, Marathon, Balemaster, G-Baler, Sierra, IPS and more.
Fluent Conveyors can offer any color required to meet your project specifications. Please let a Fluent Conveyors employee know the RAL number for the paint as well as the paint manufacturer (Sherwin-Williams, PPG, Valspar, Diamond Vogel etc.). You can also send us in a chip sample of the paint you are looking to match.
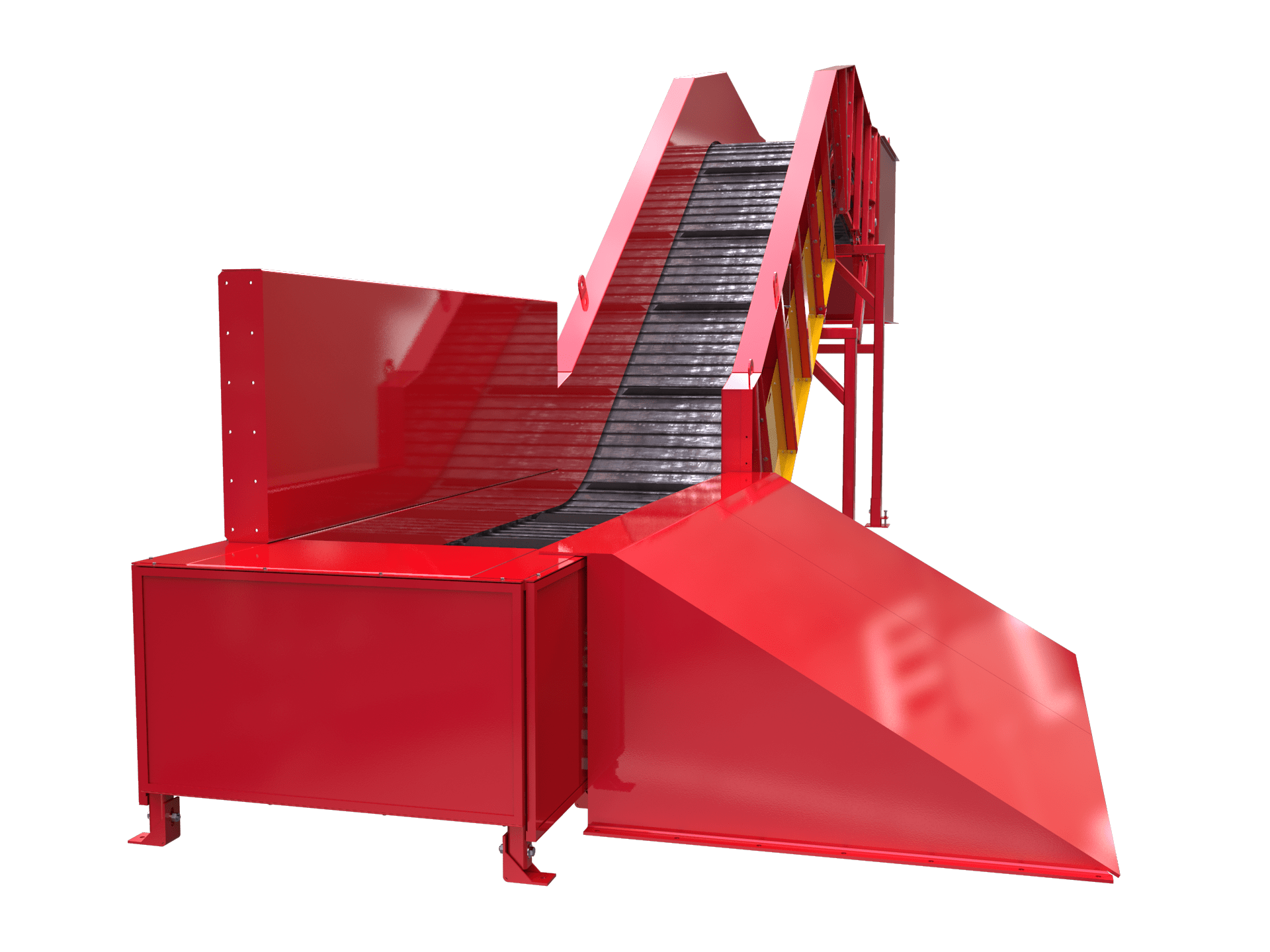
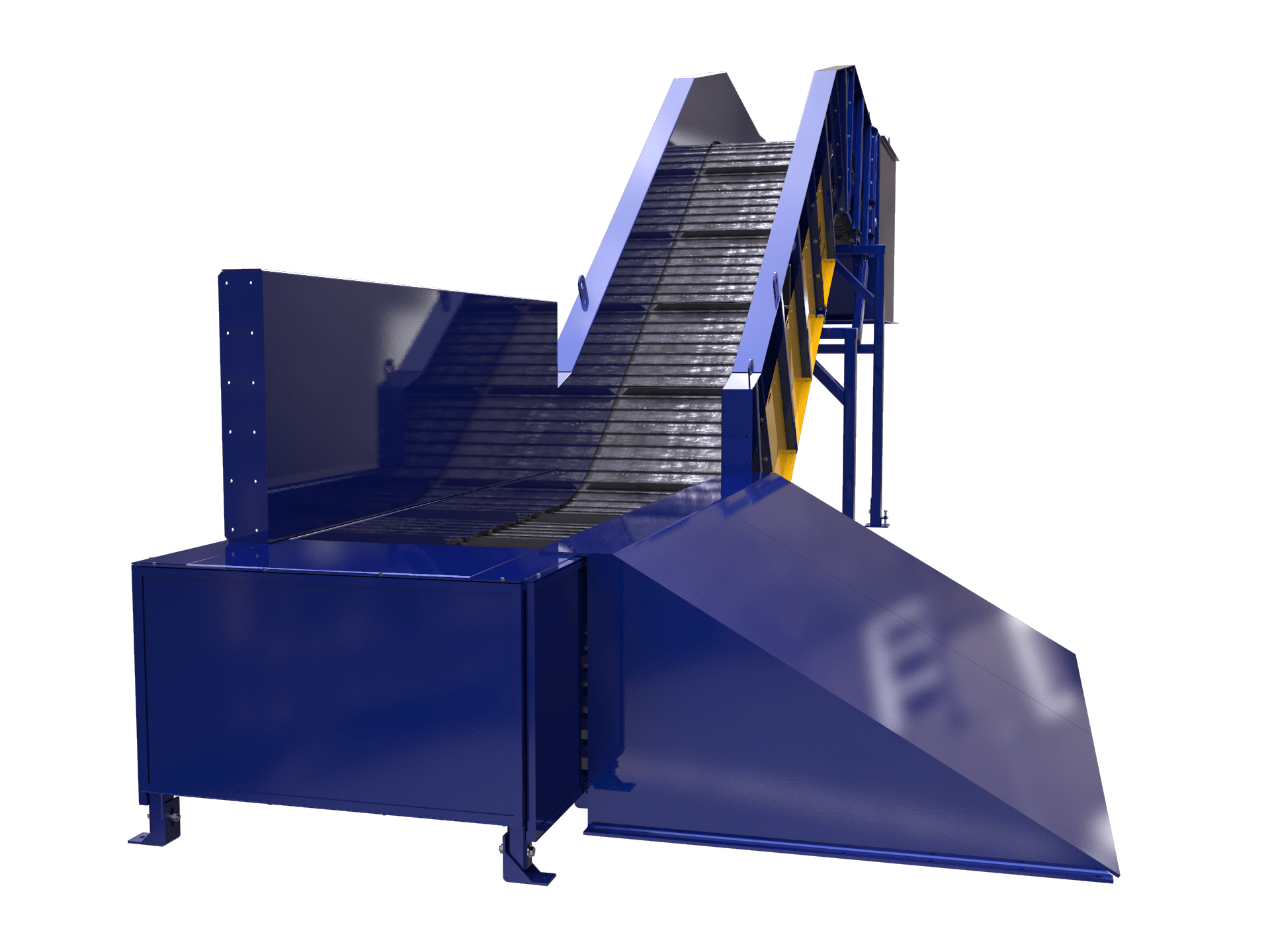
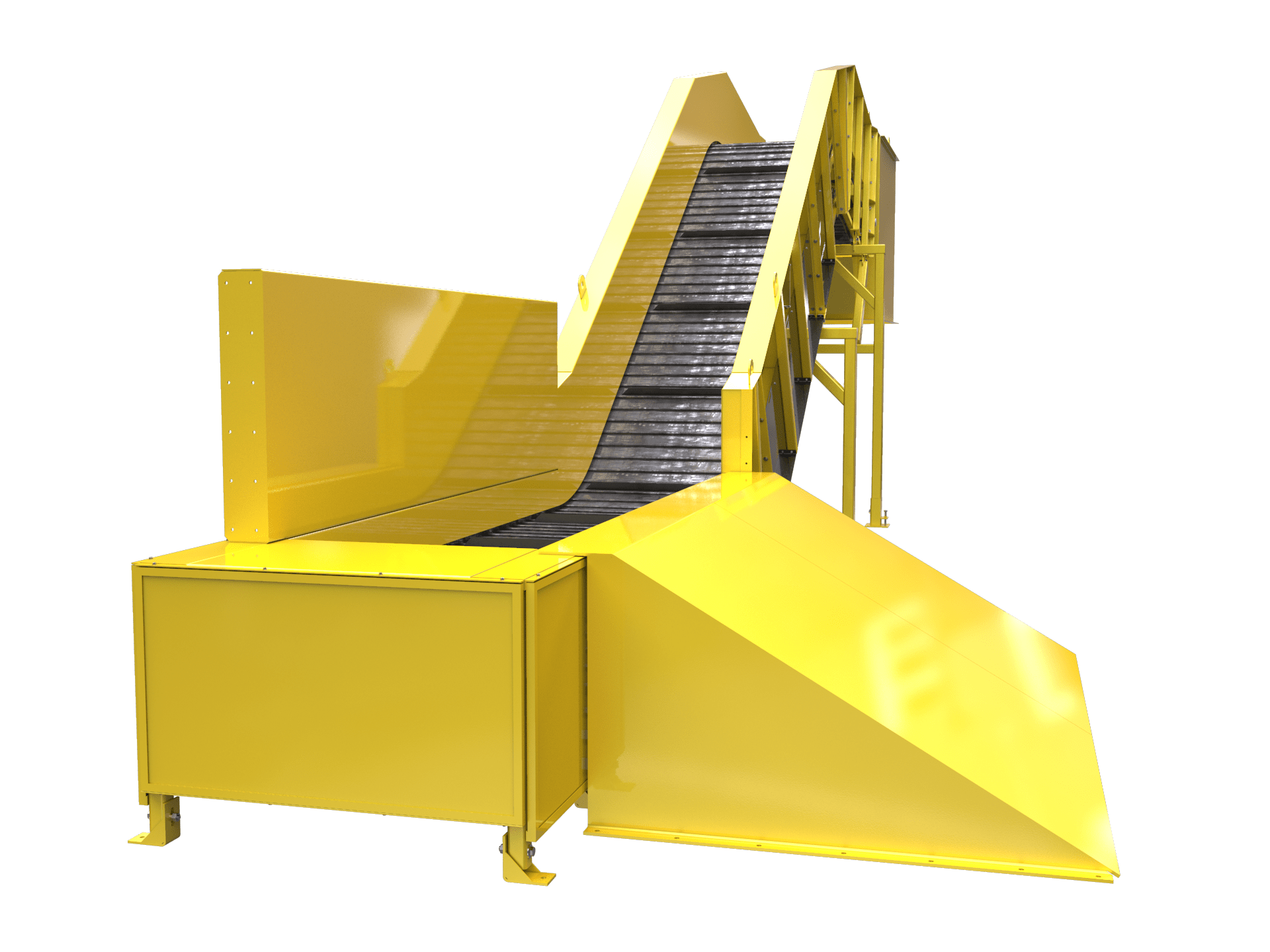
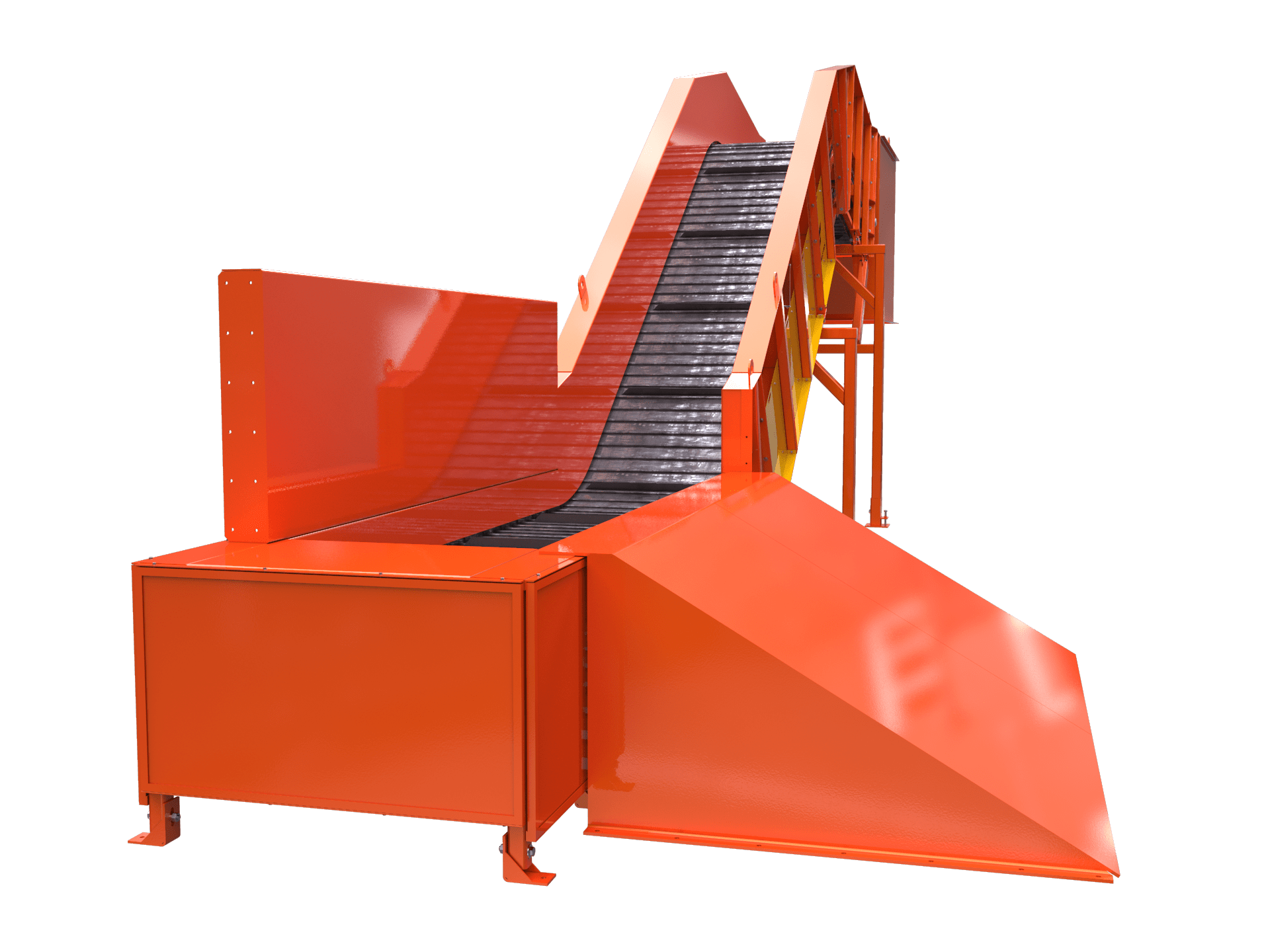
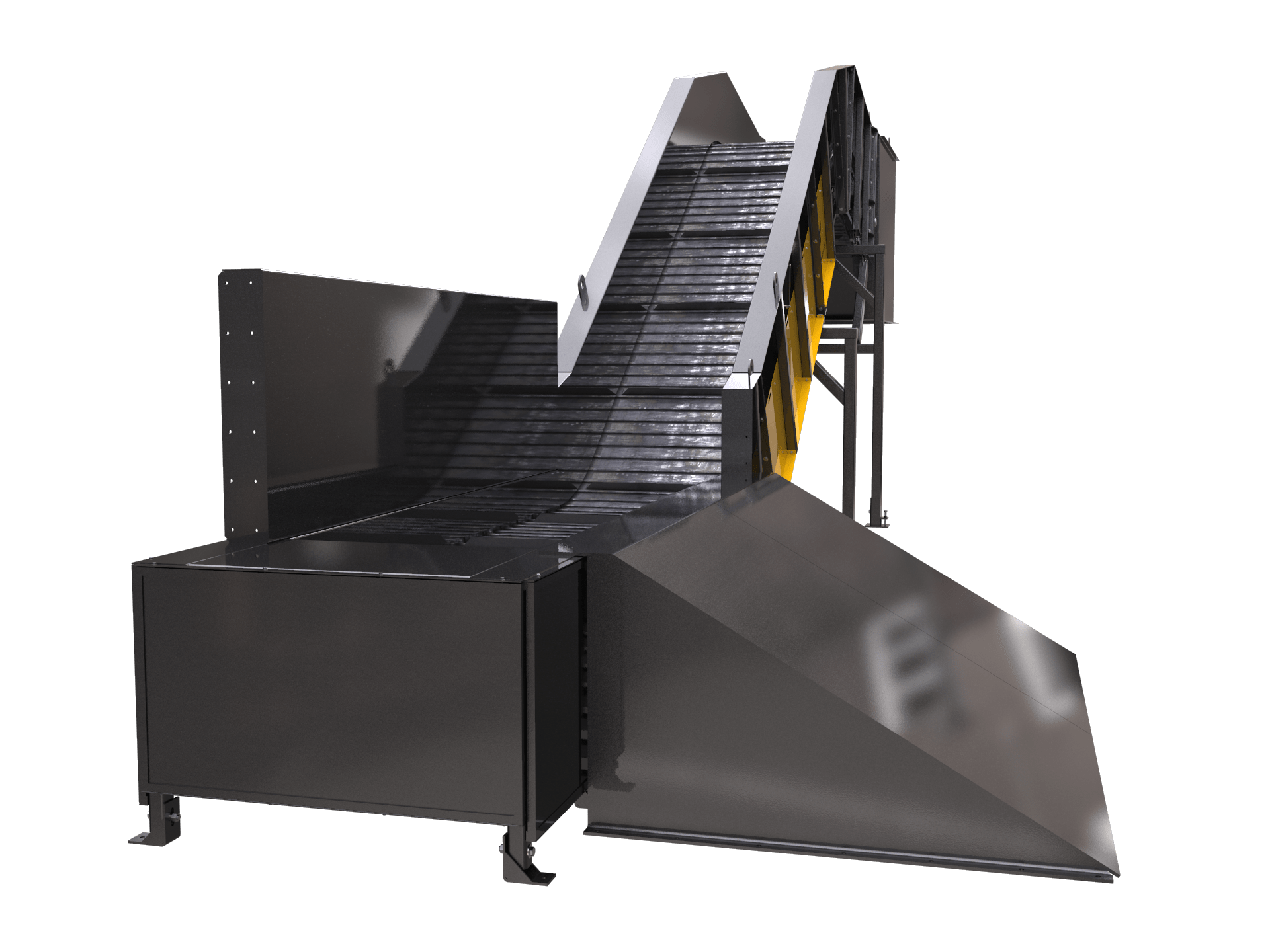
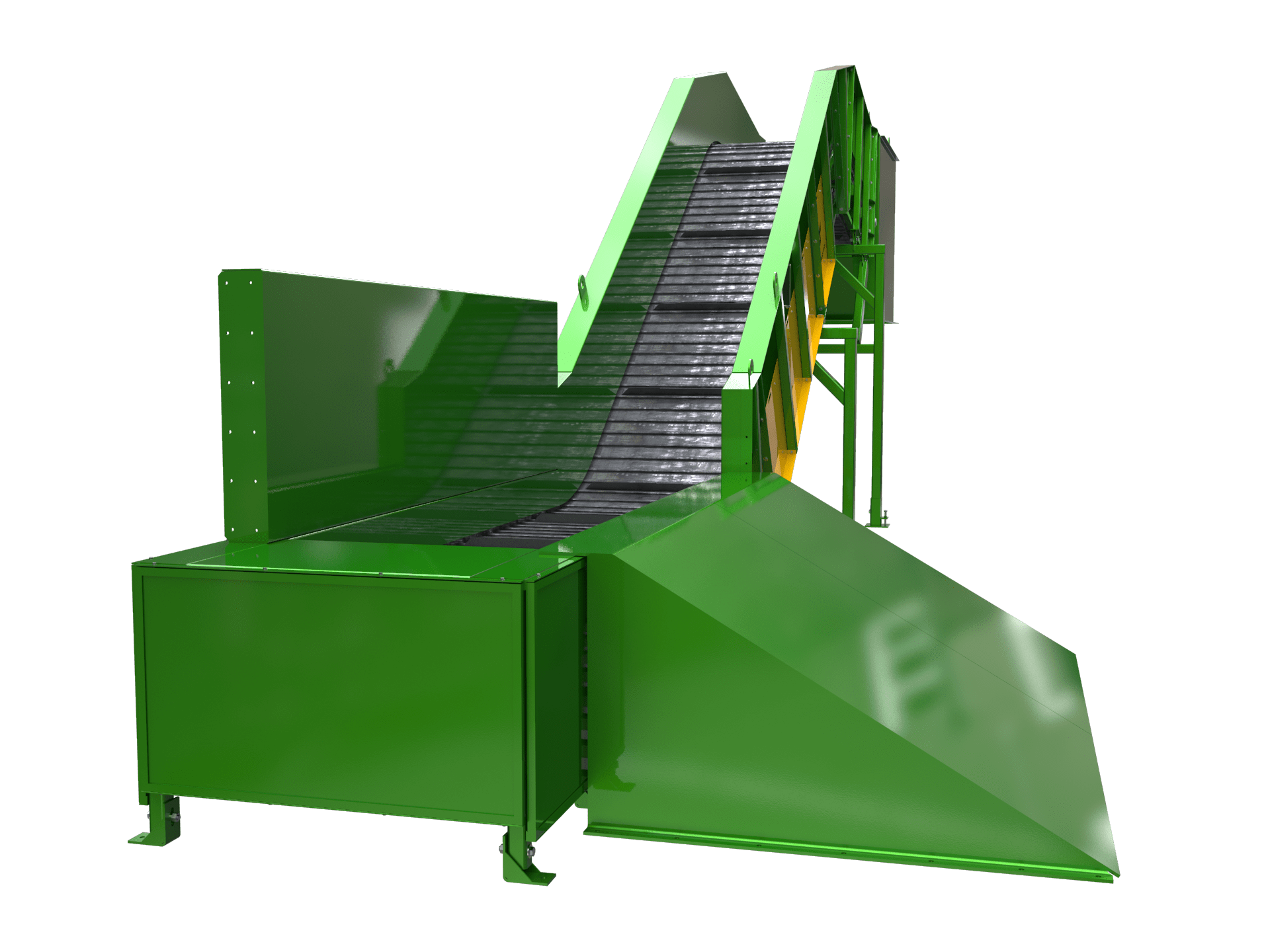
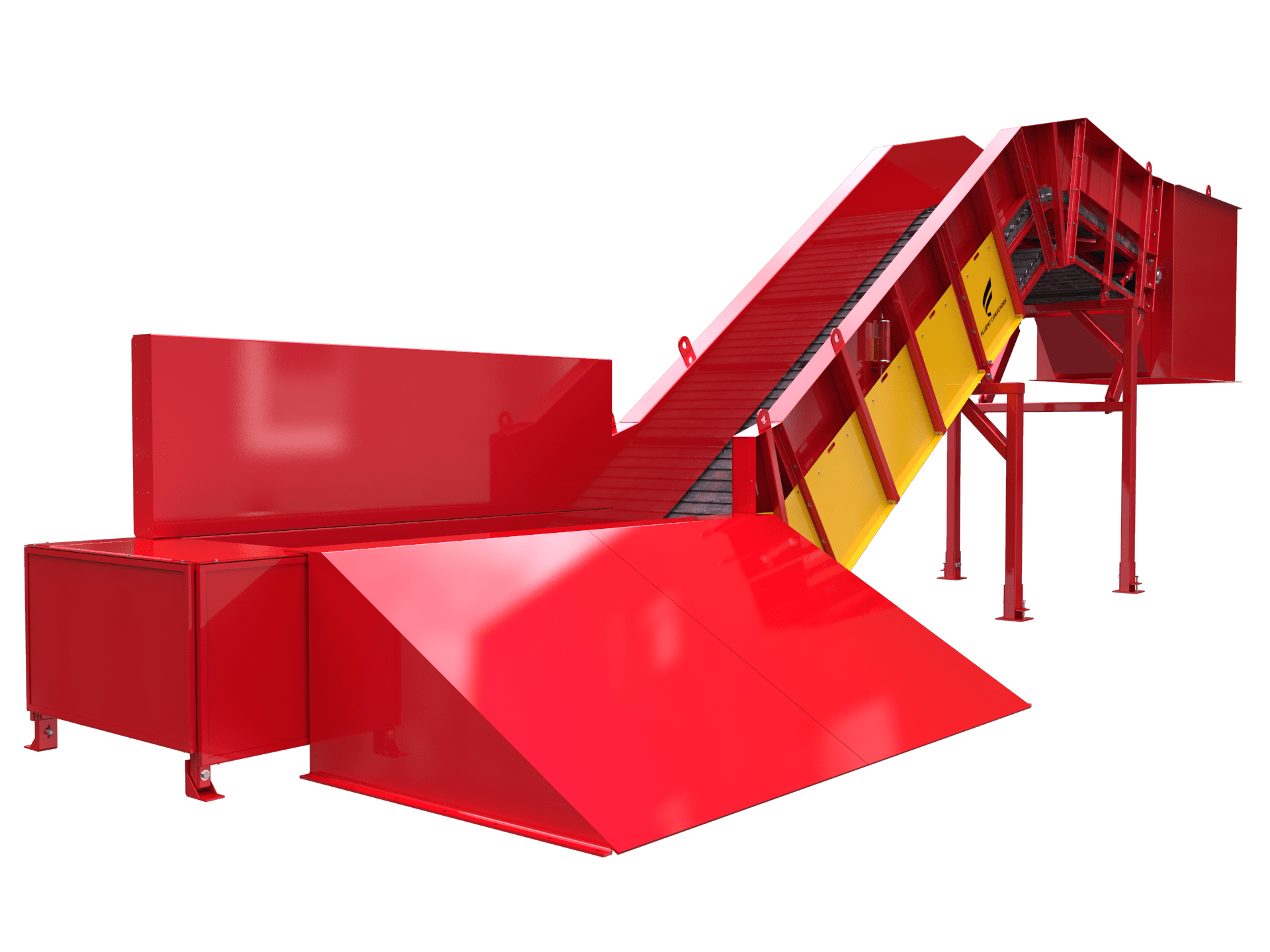
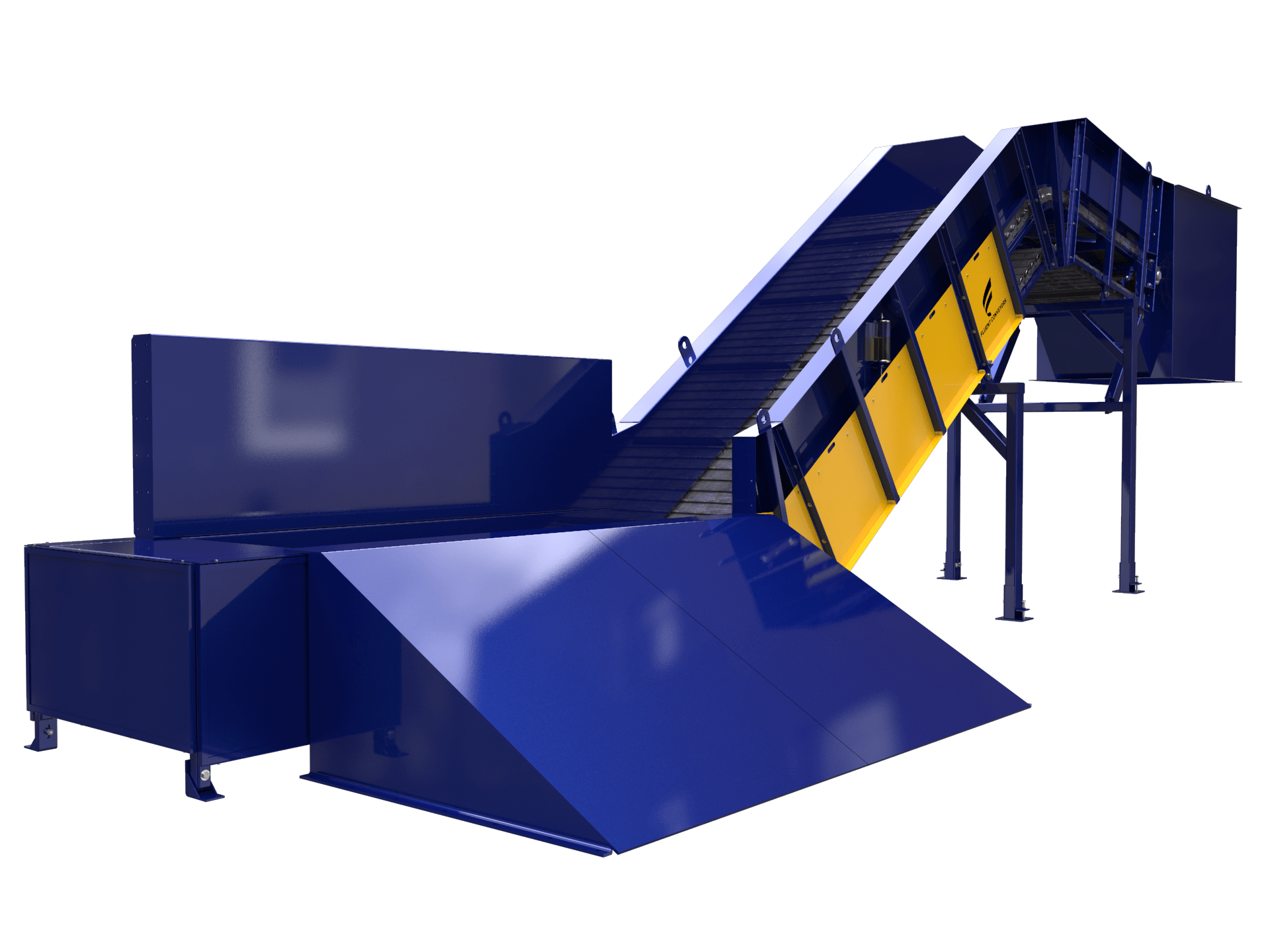
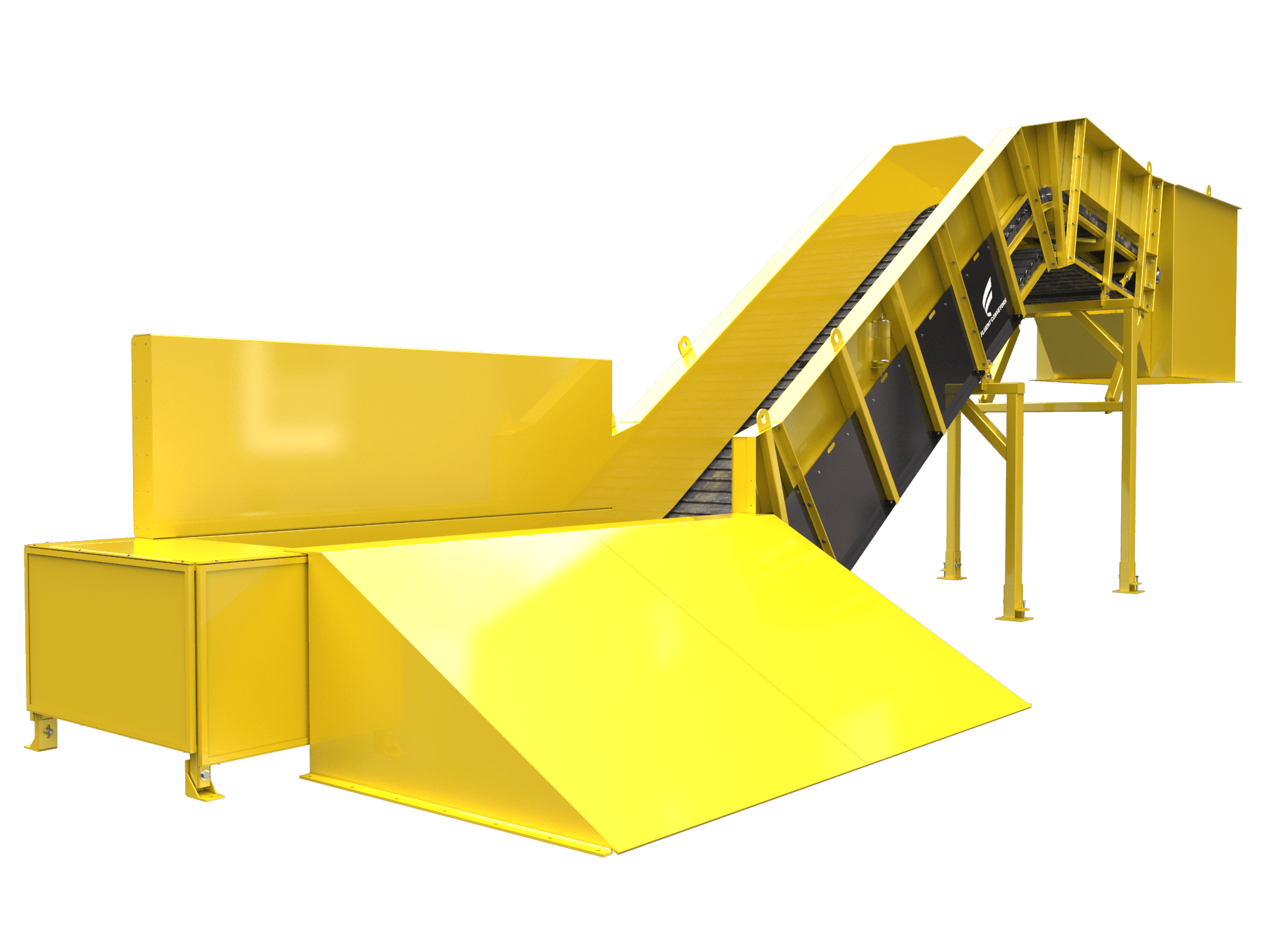
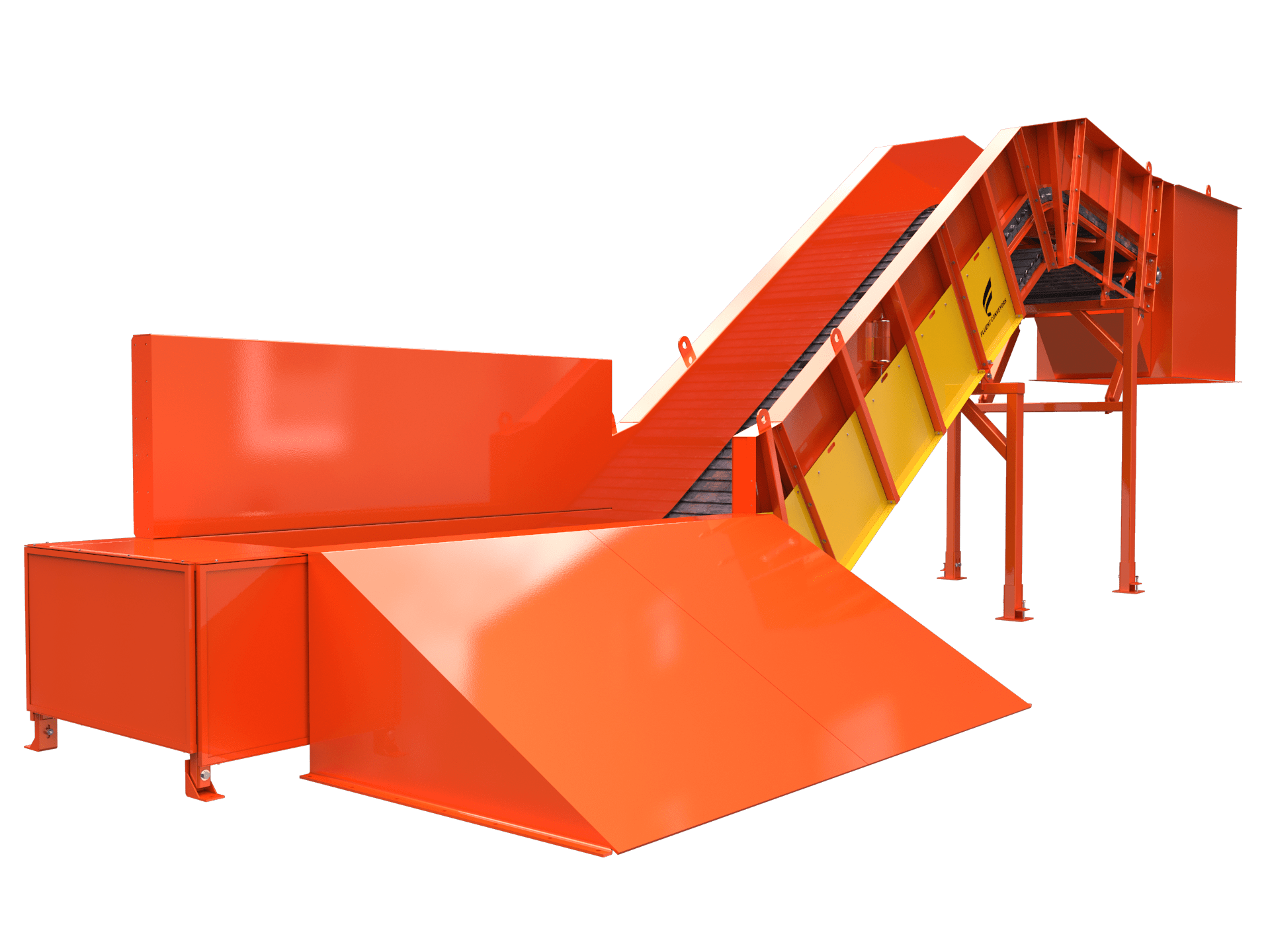
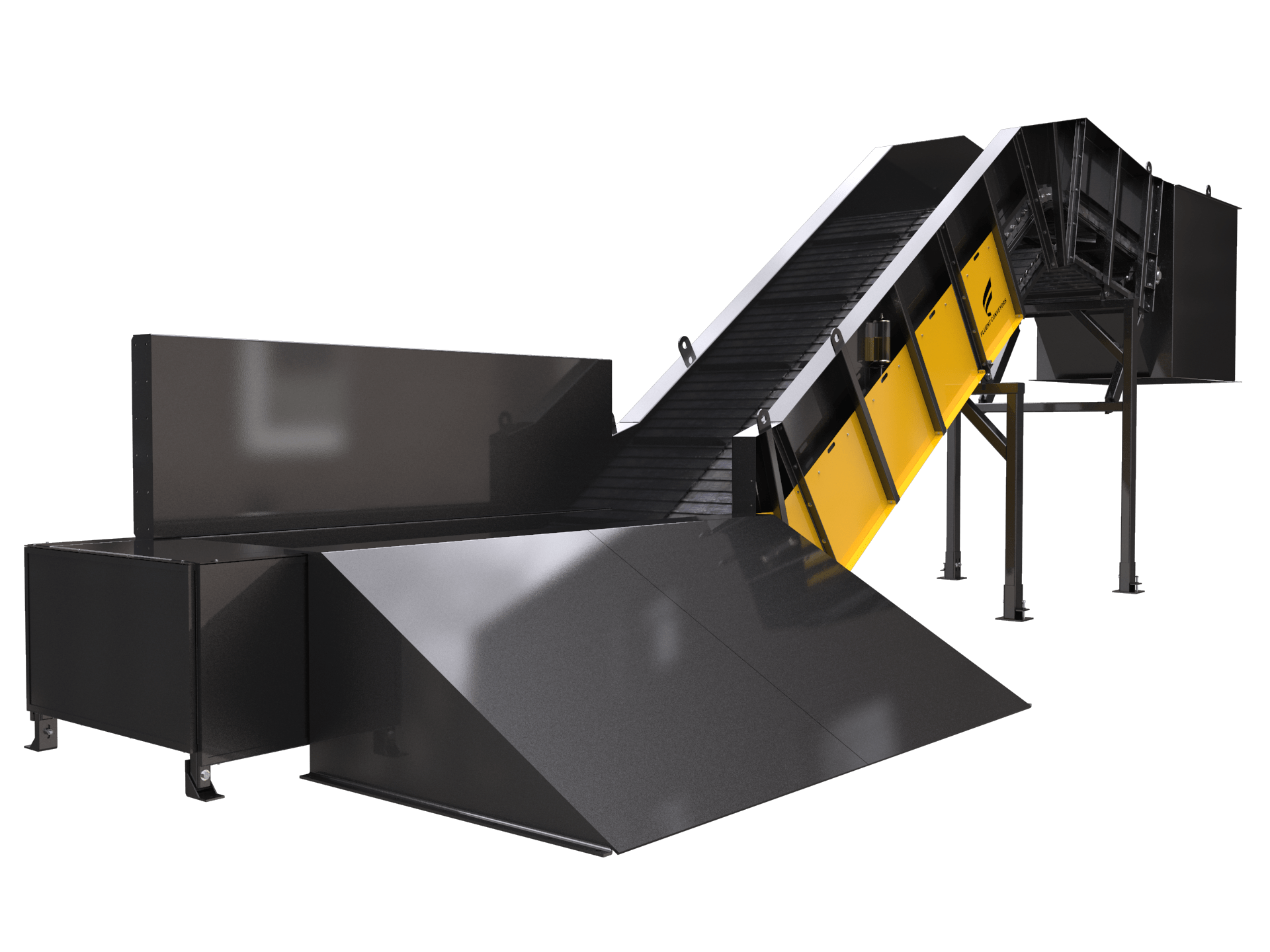
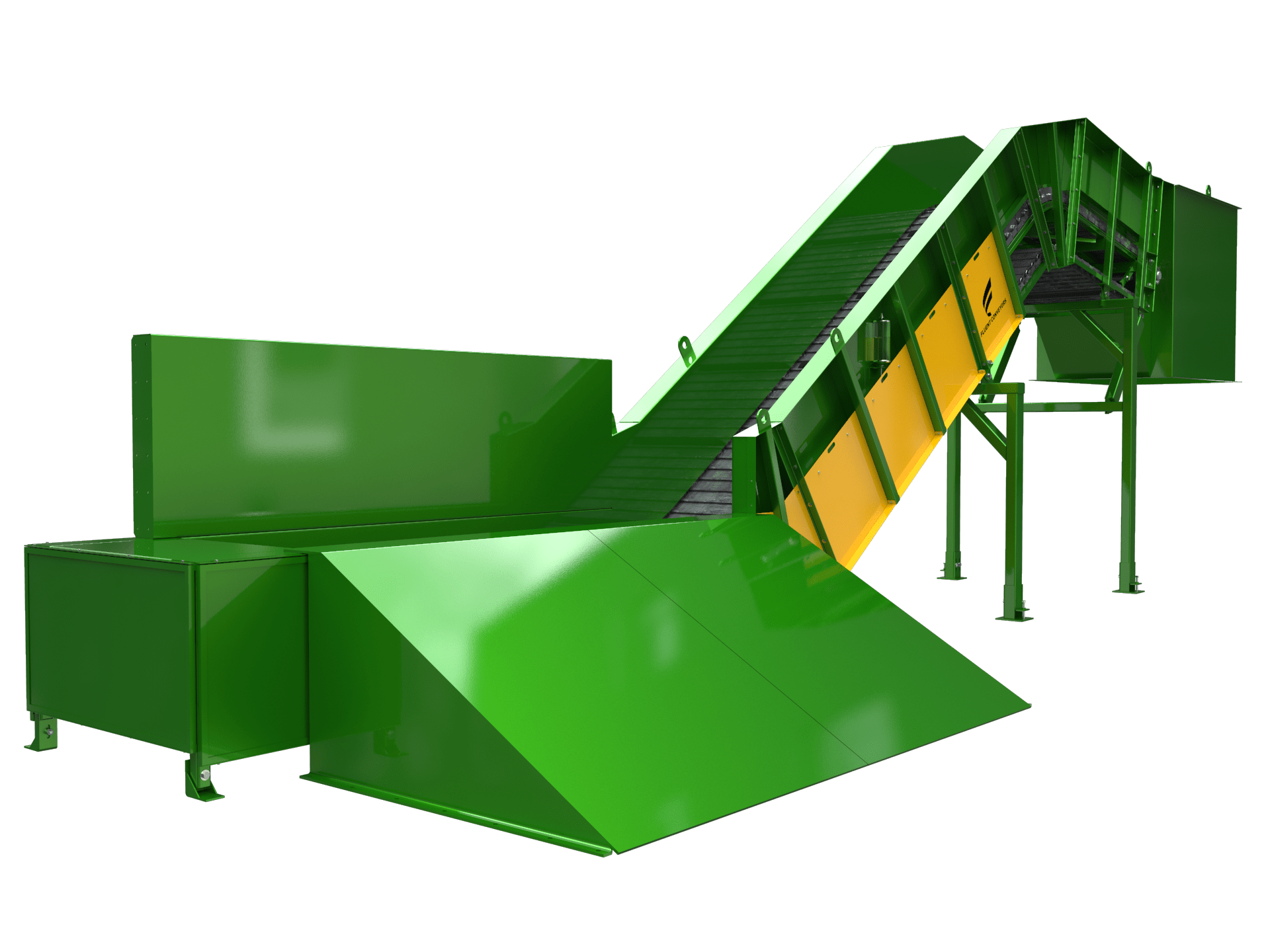
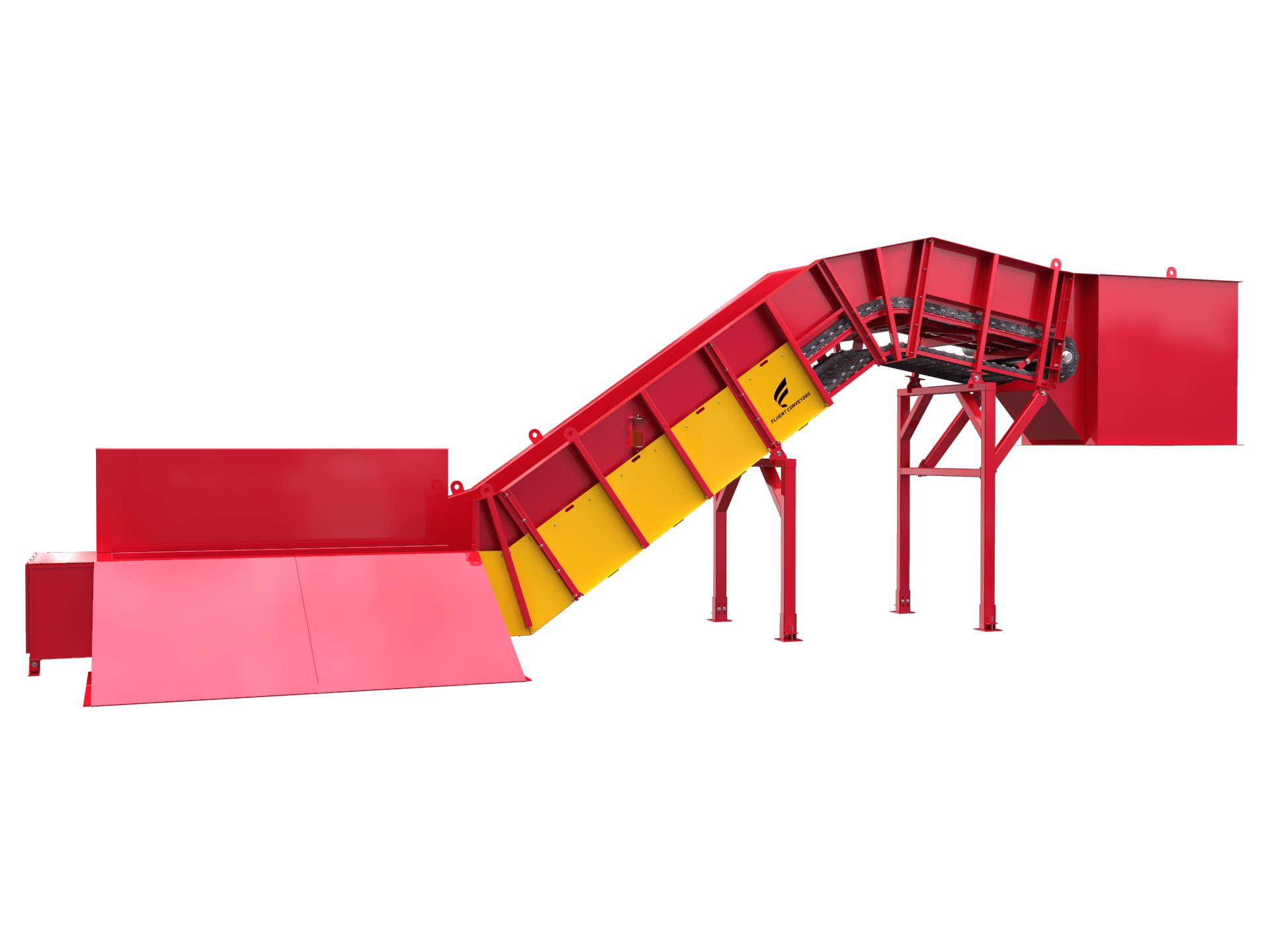
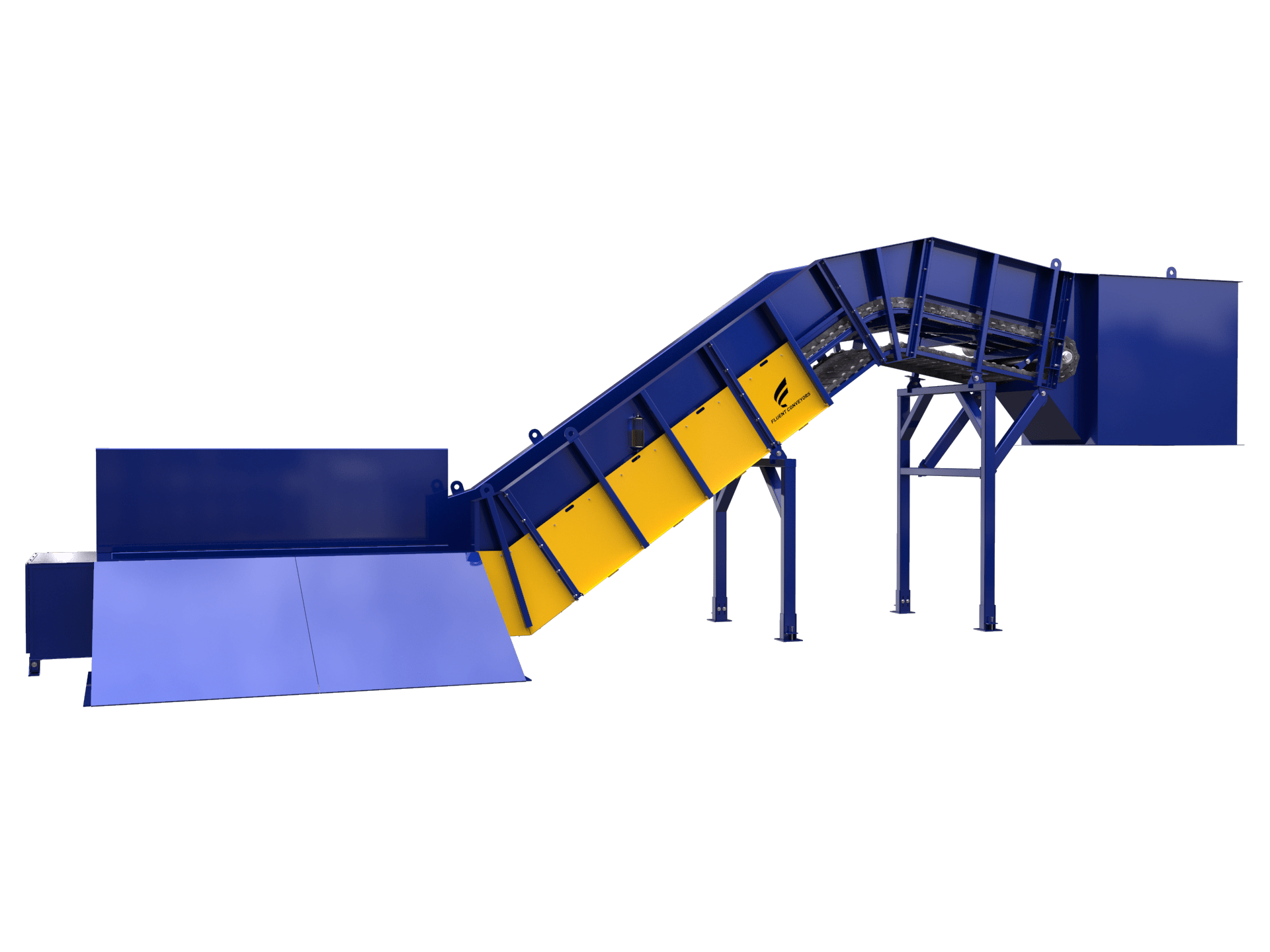
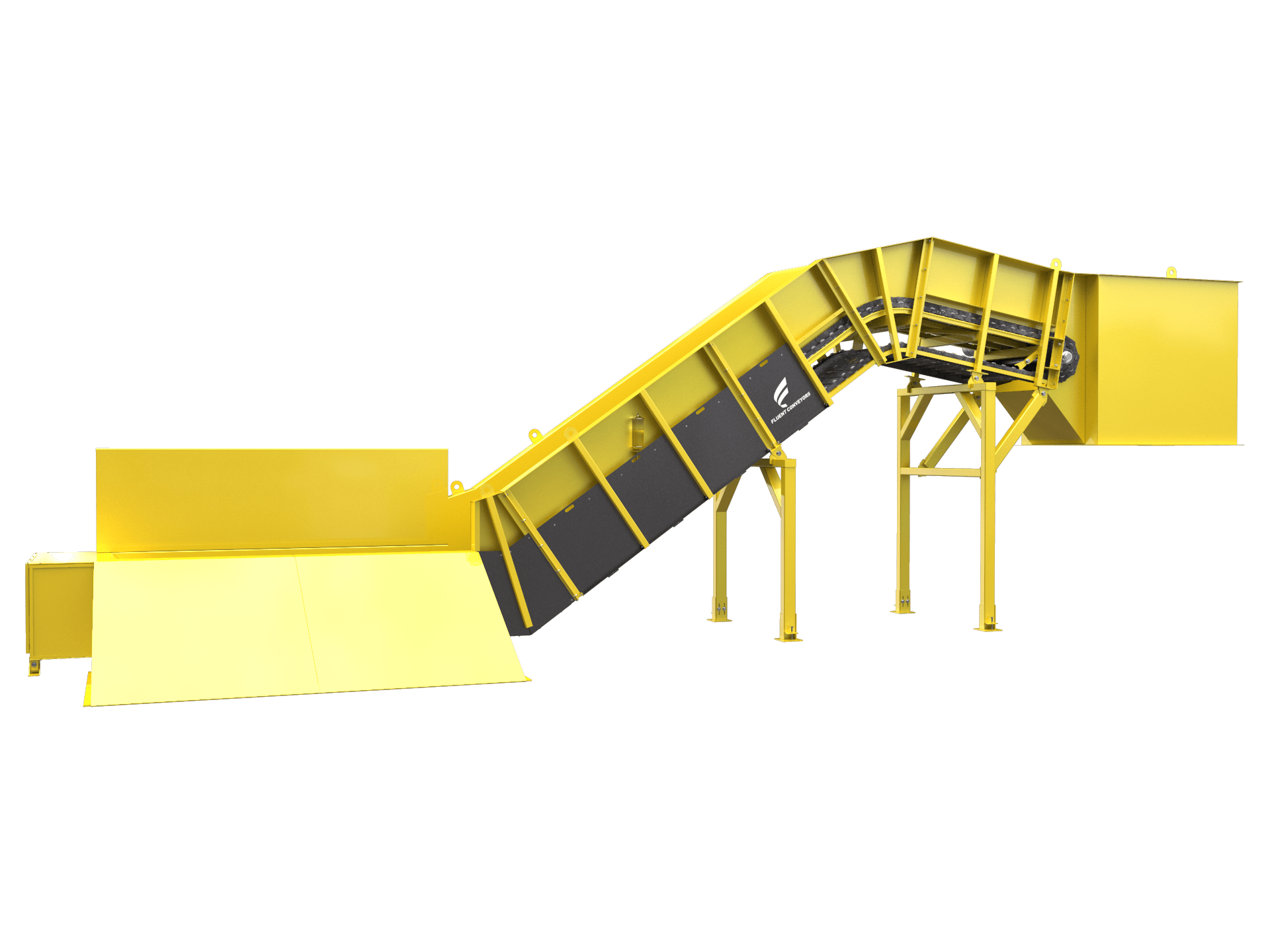
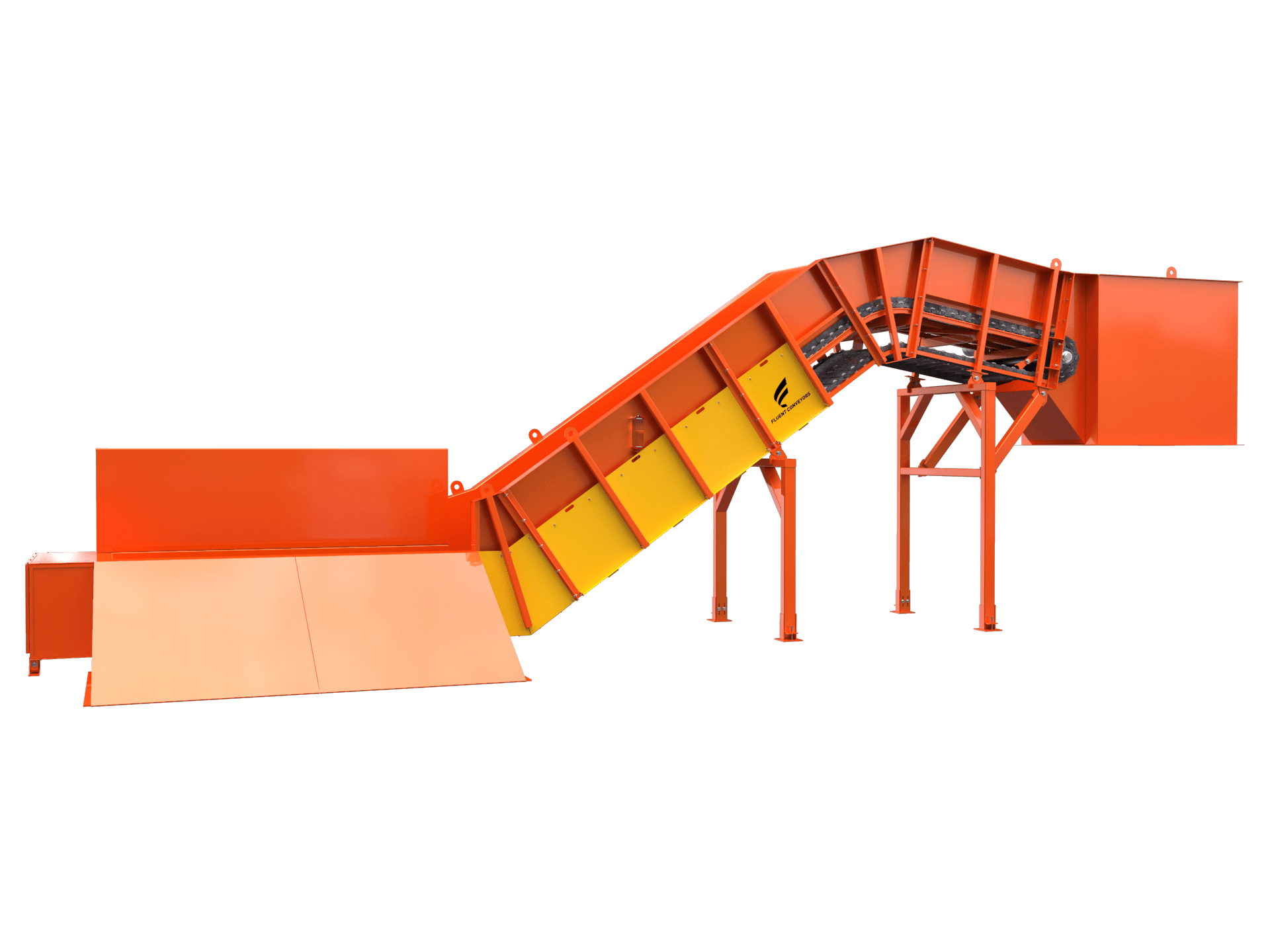
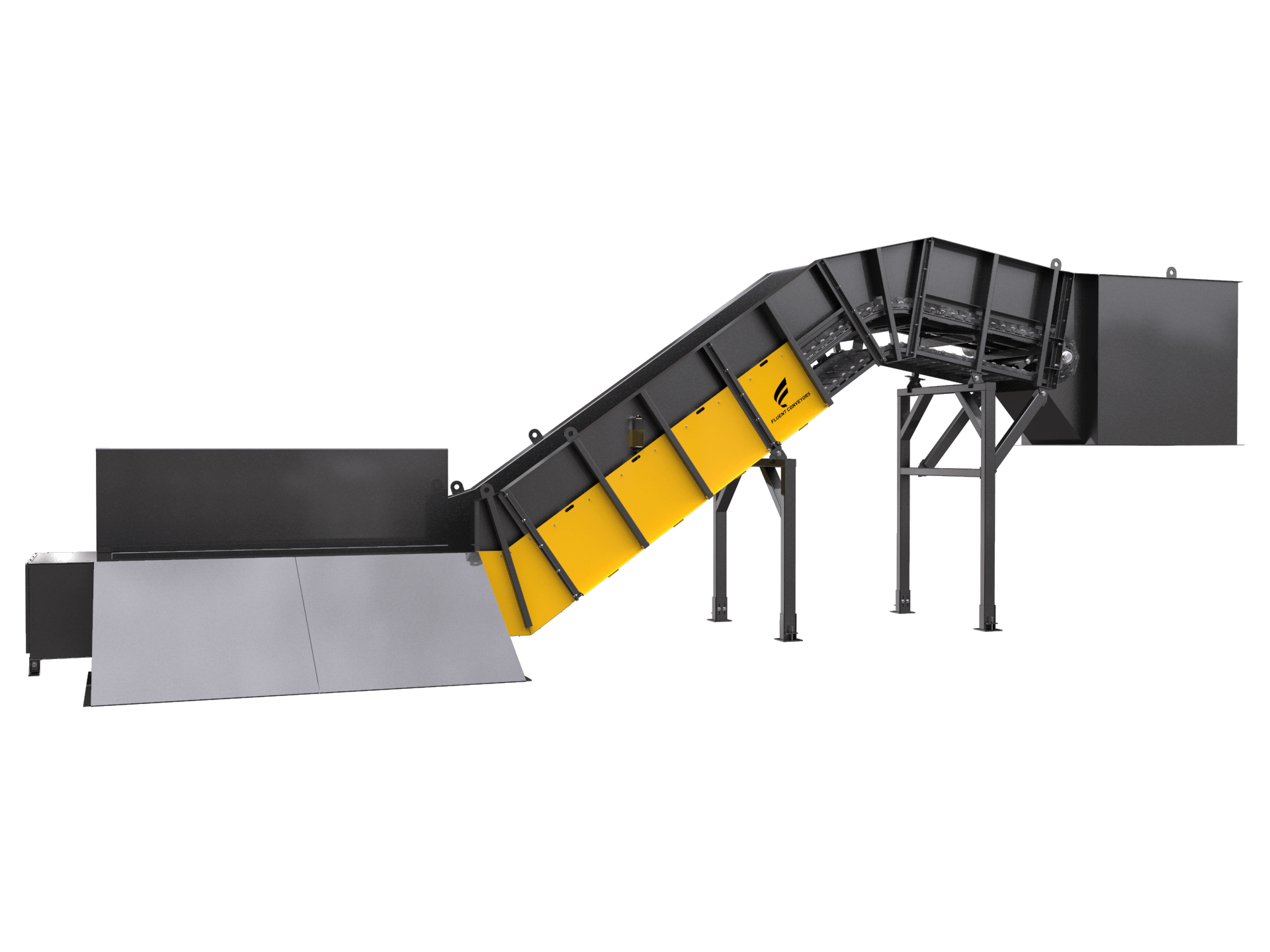
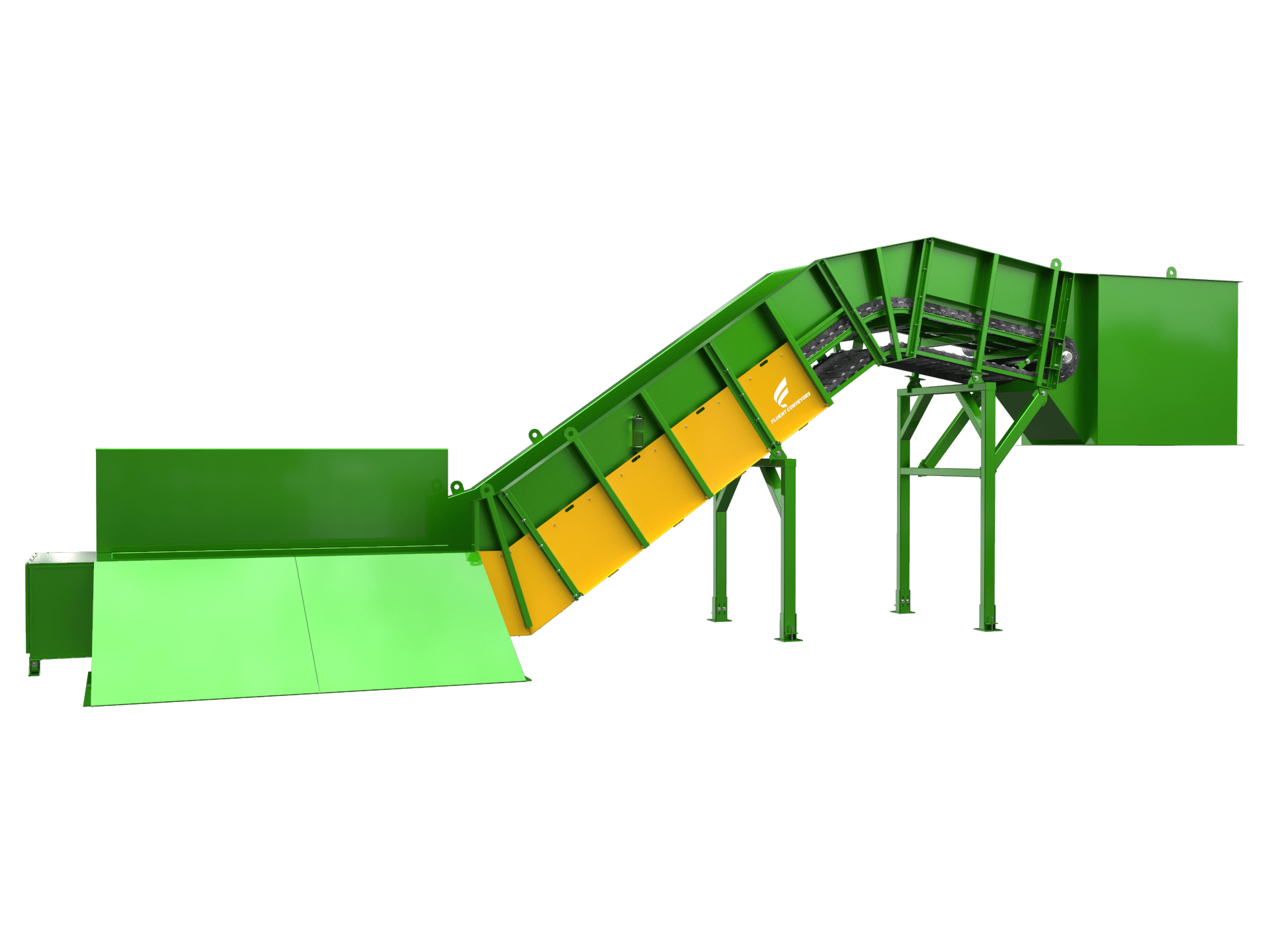
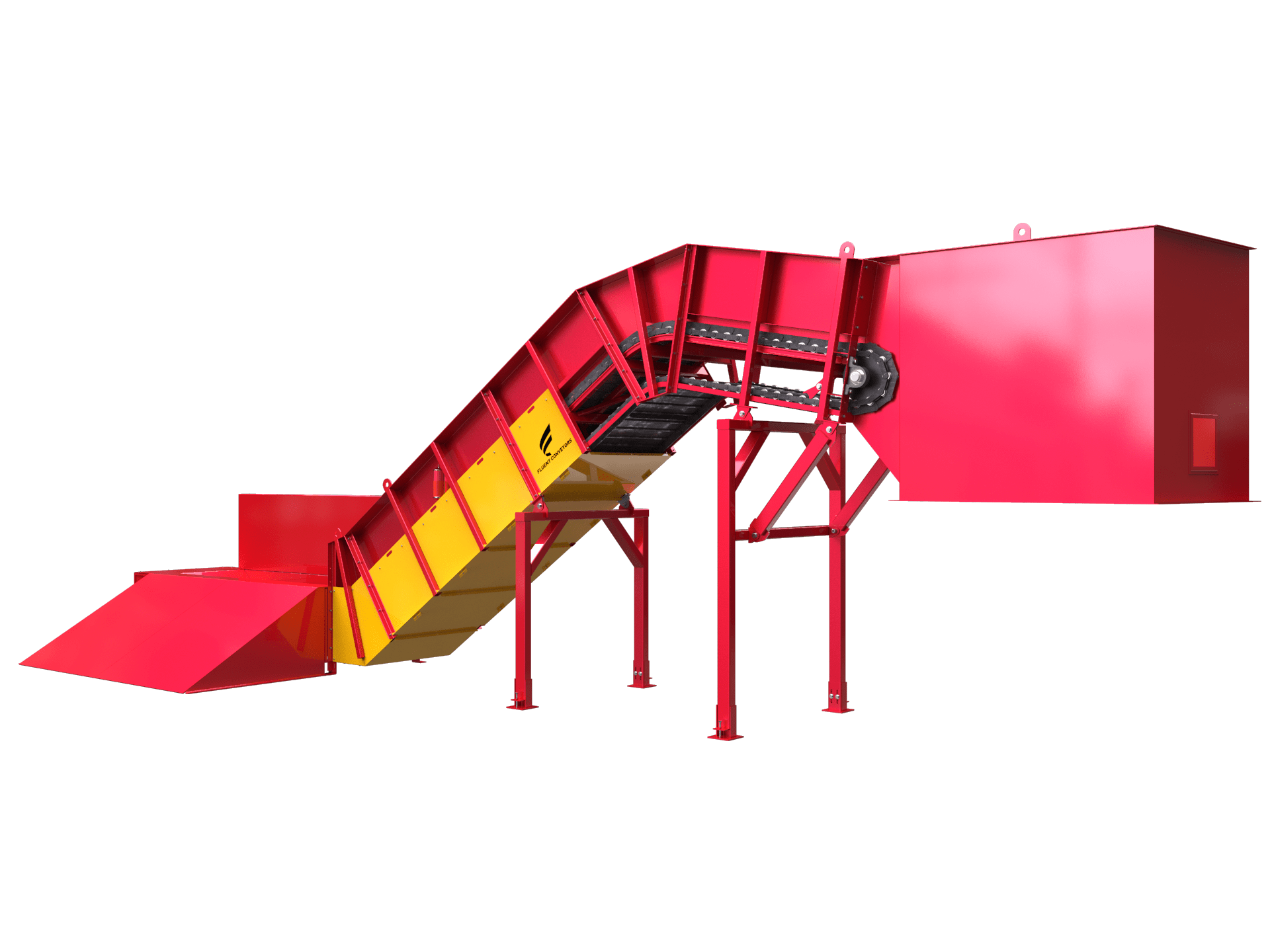
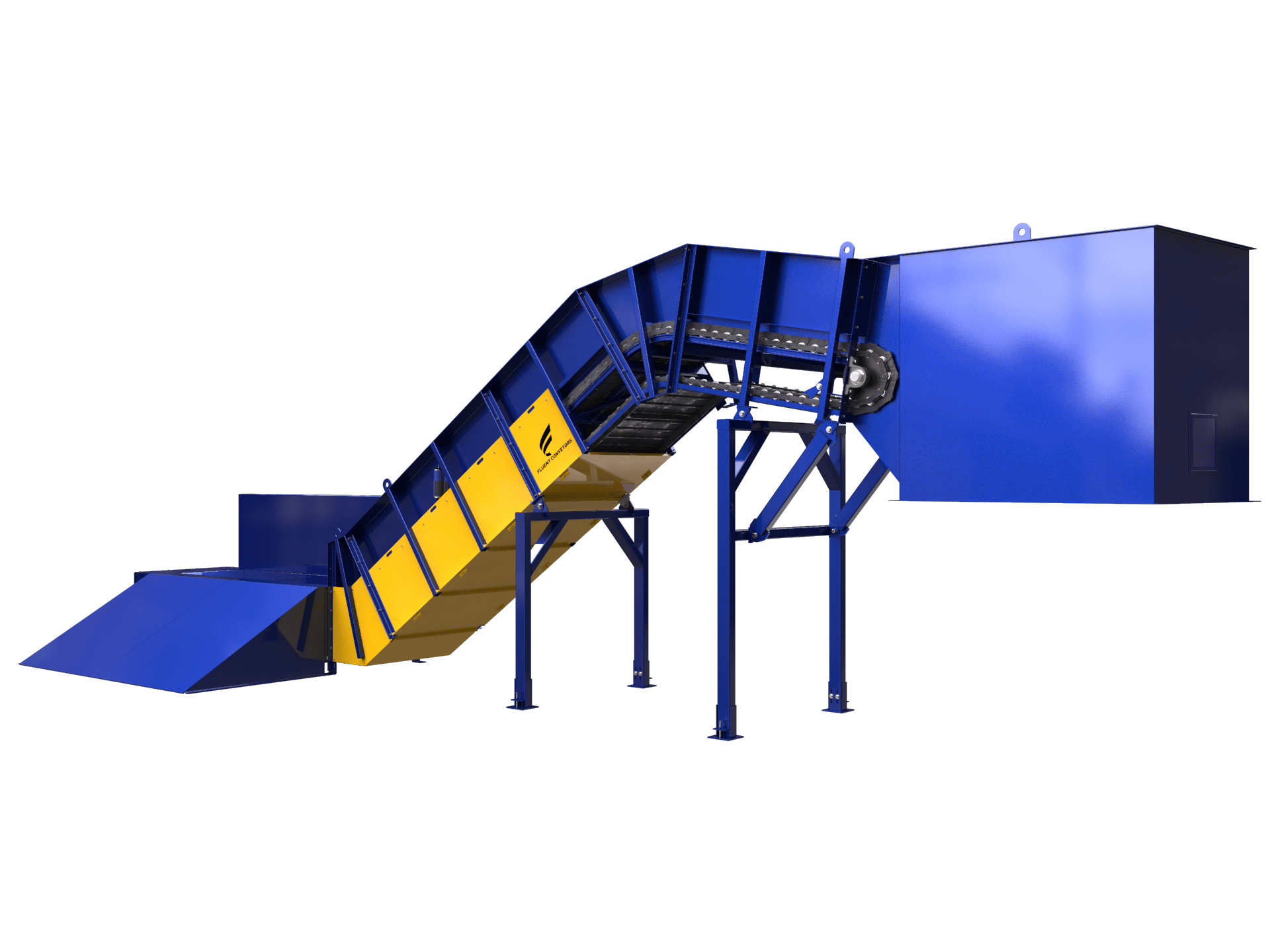
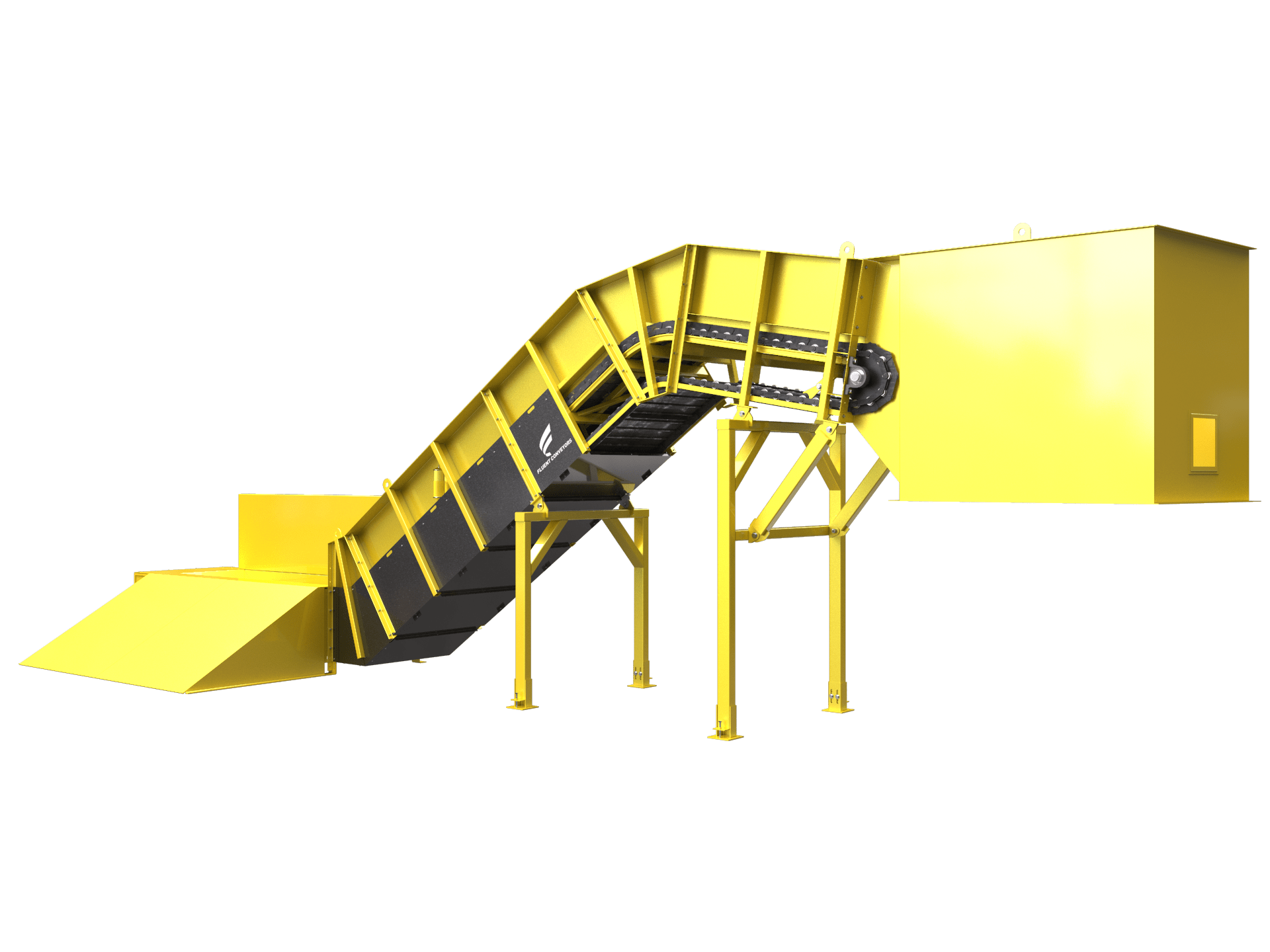
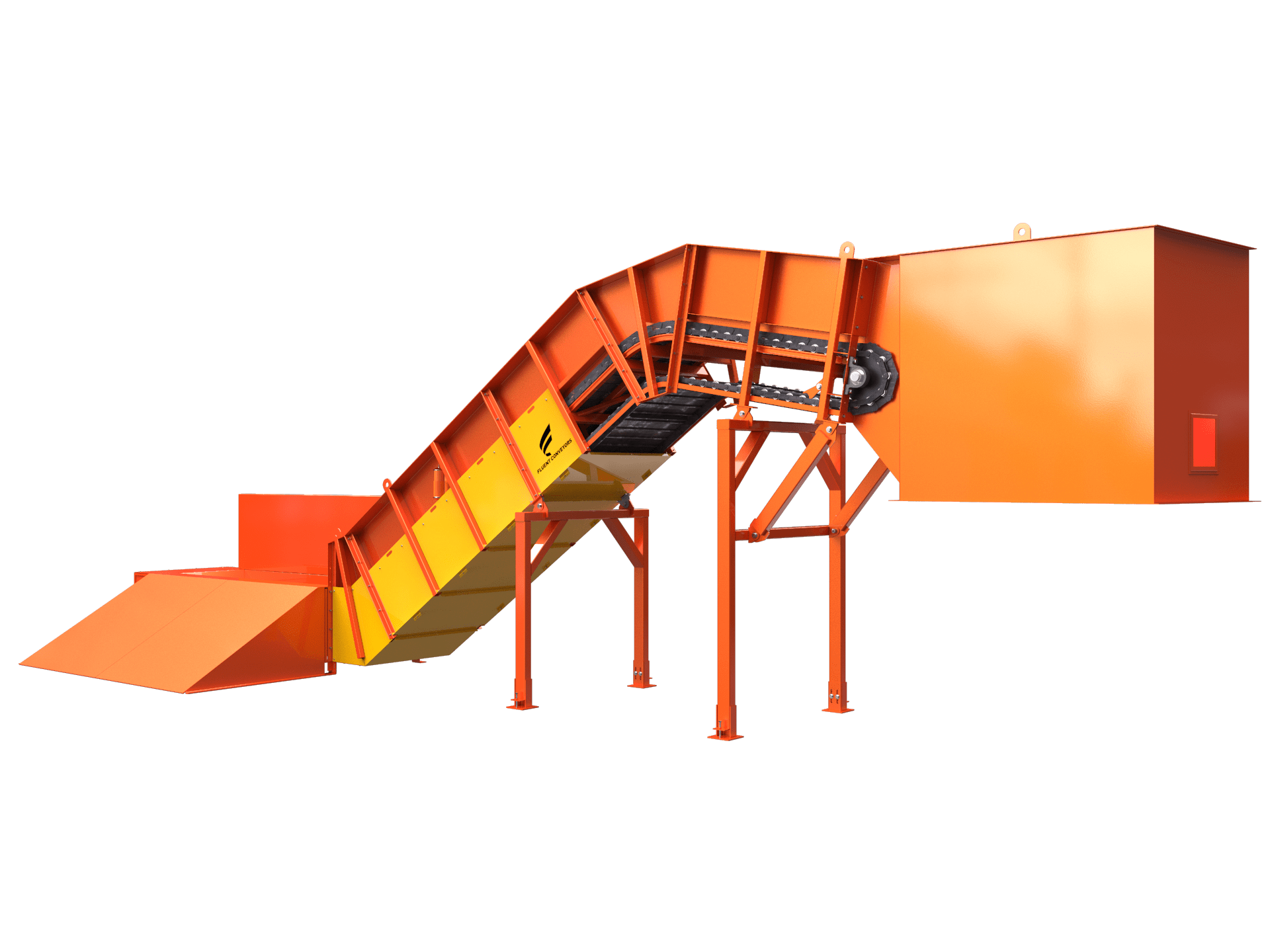
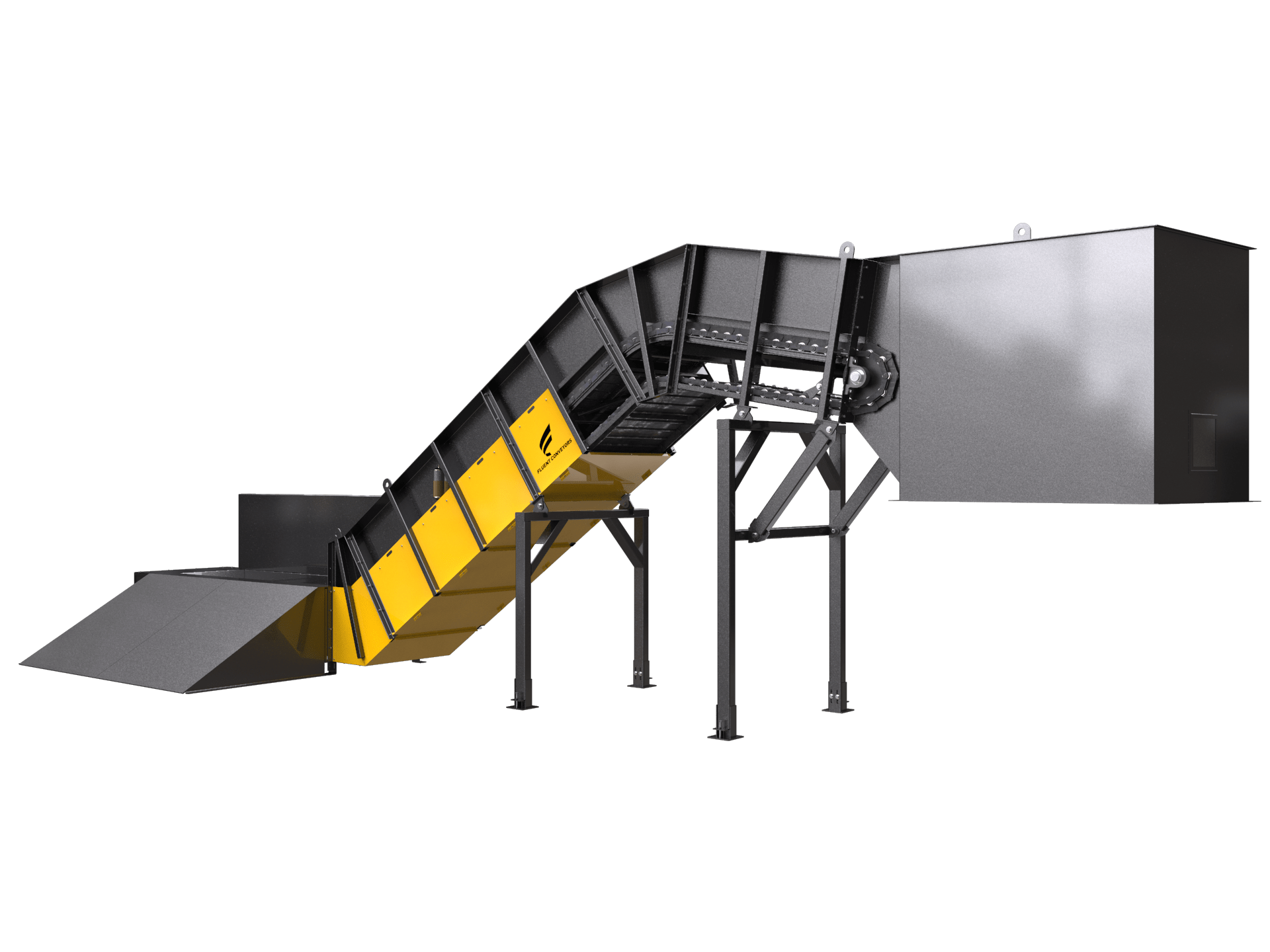
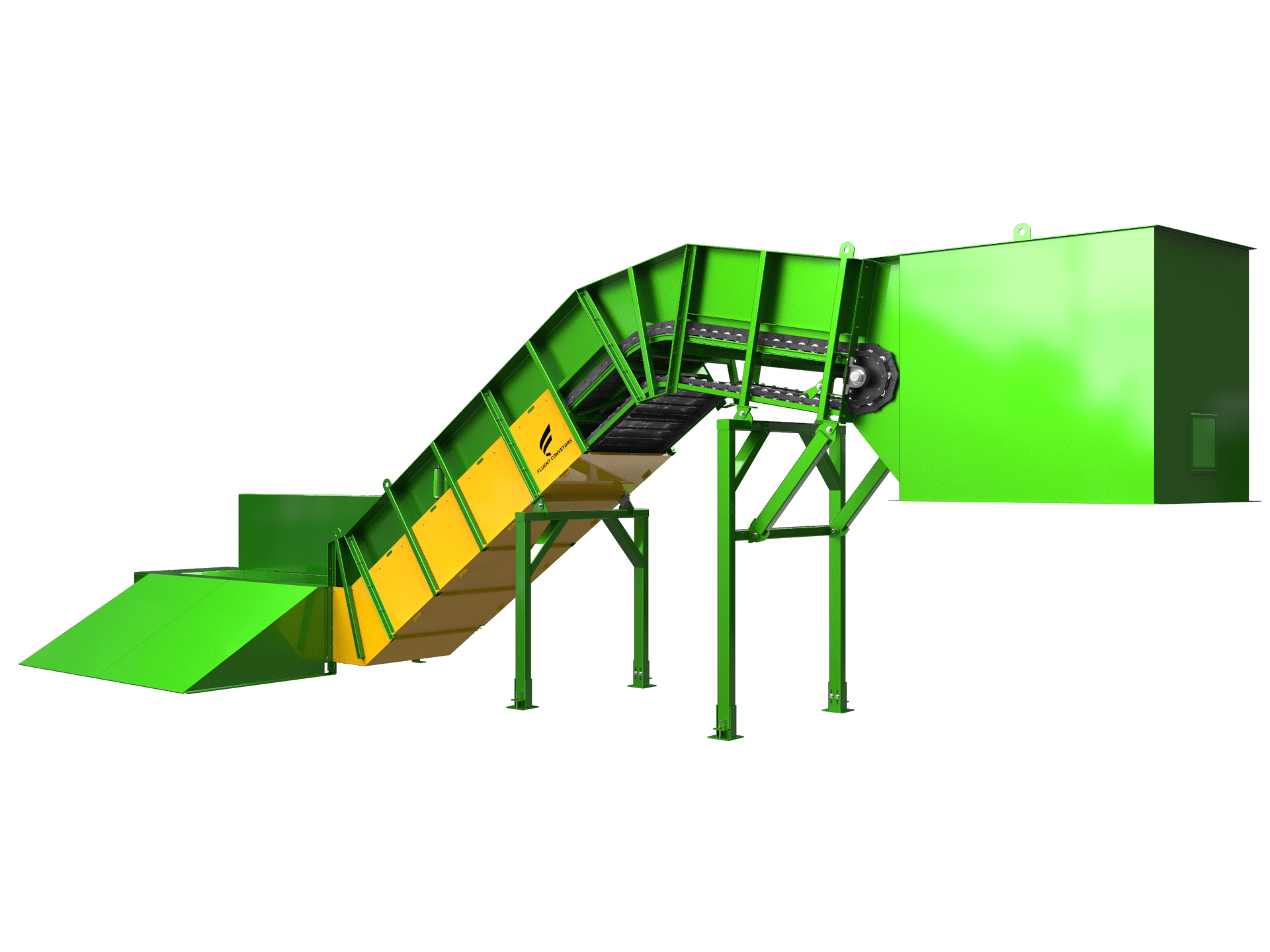
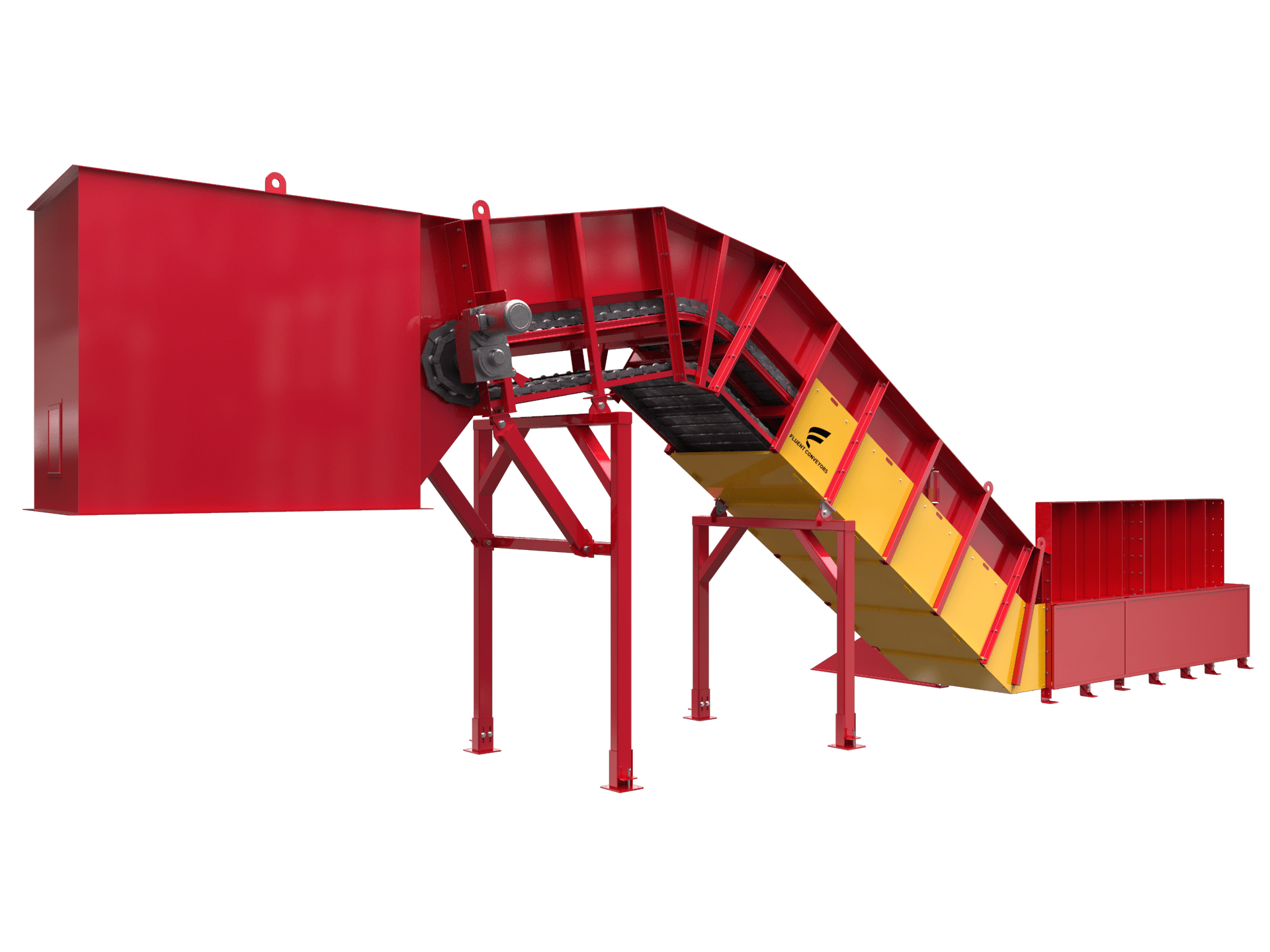
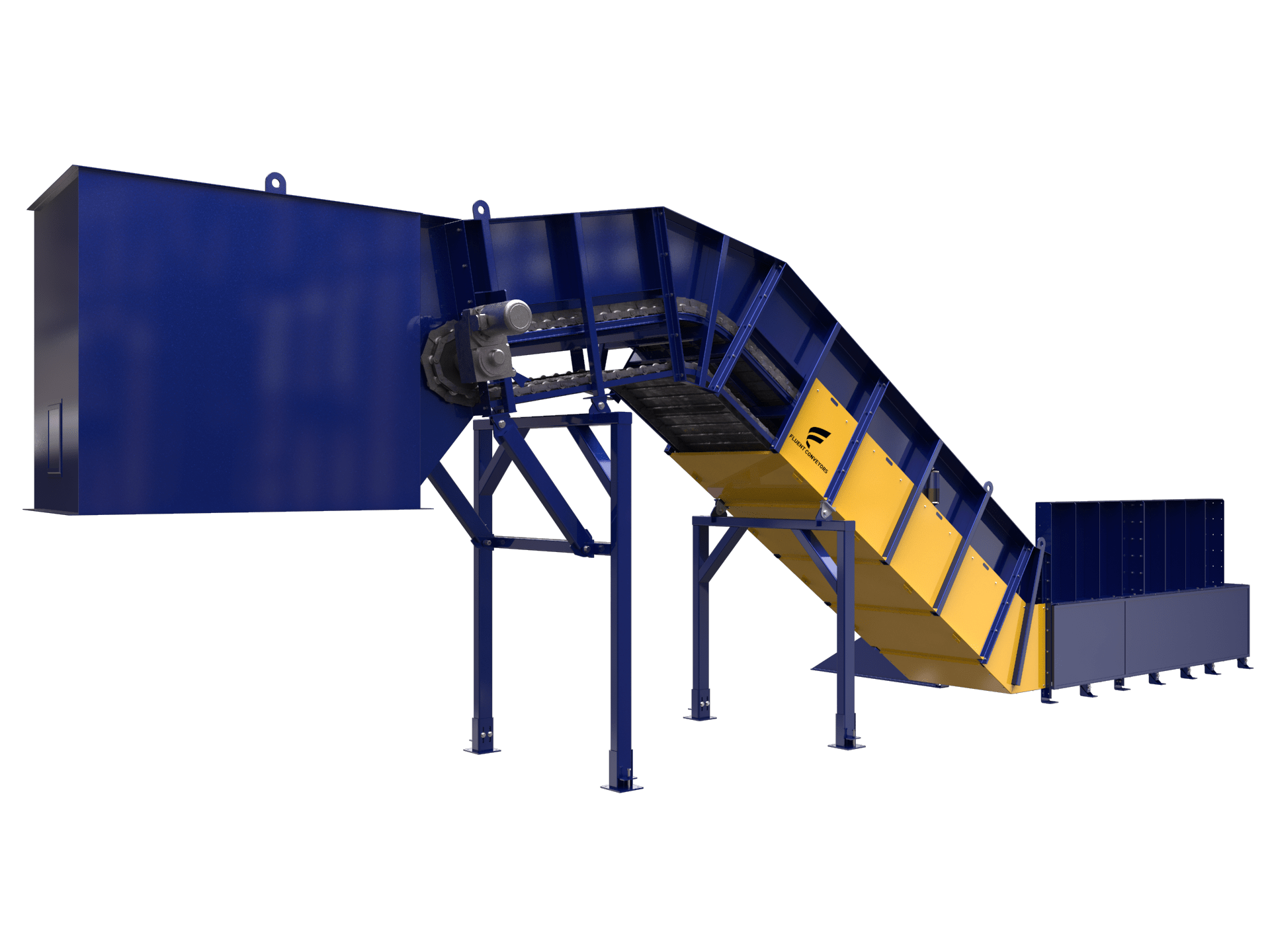
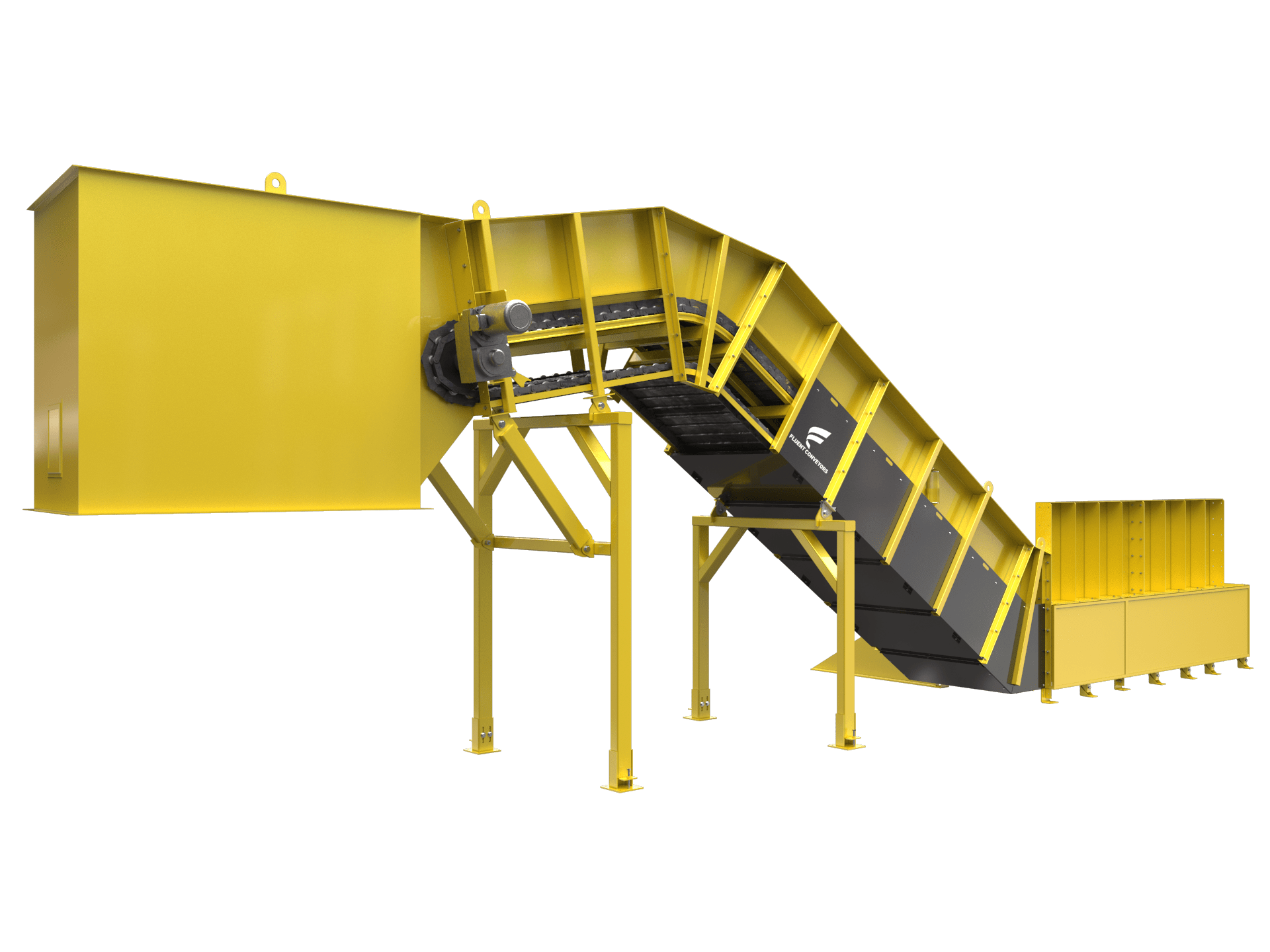
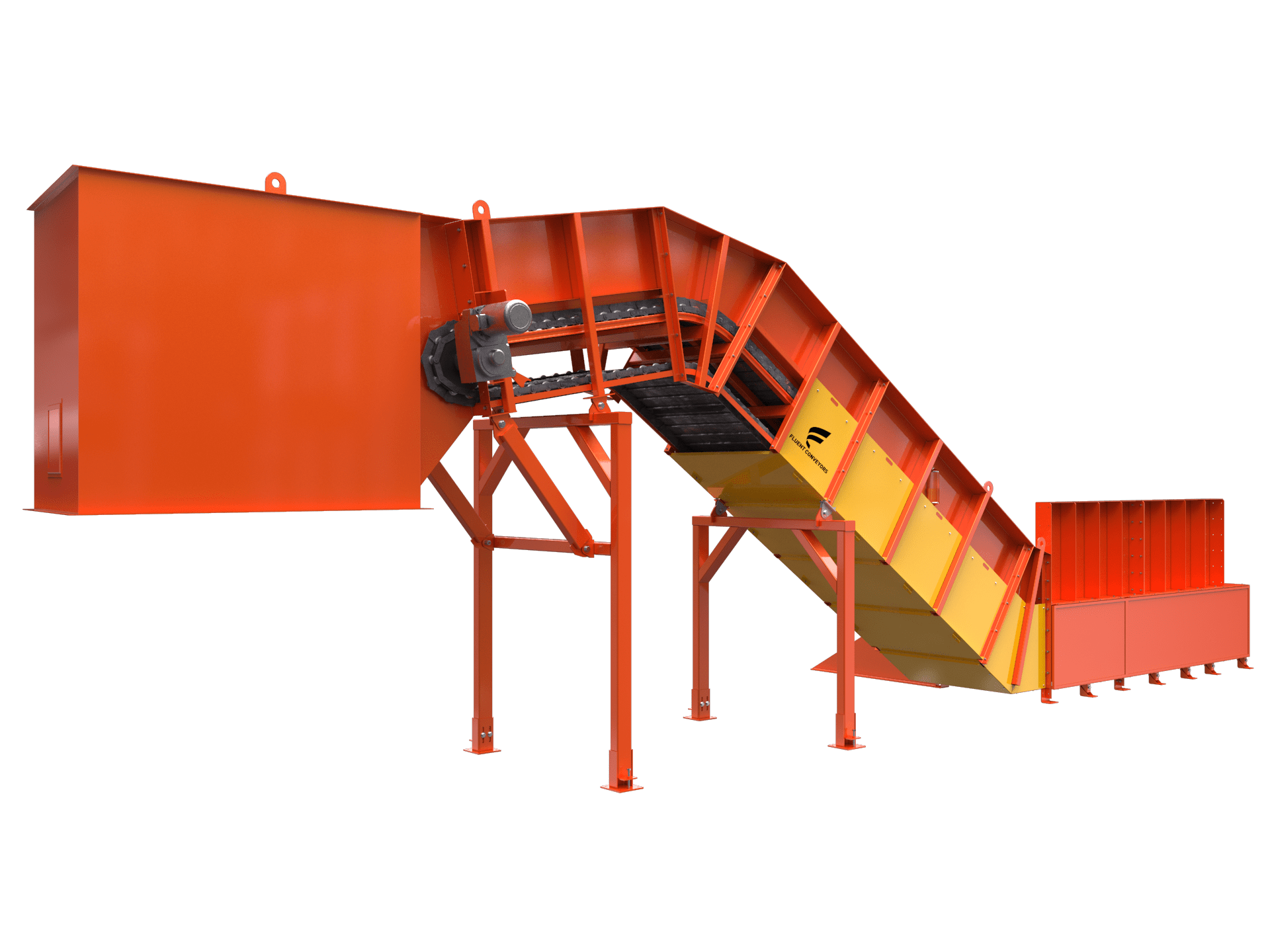
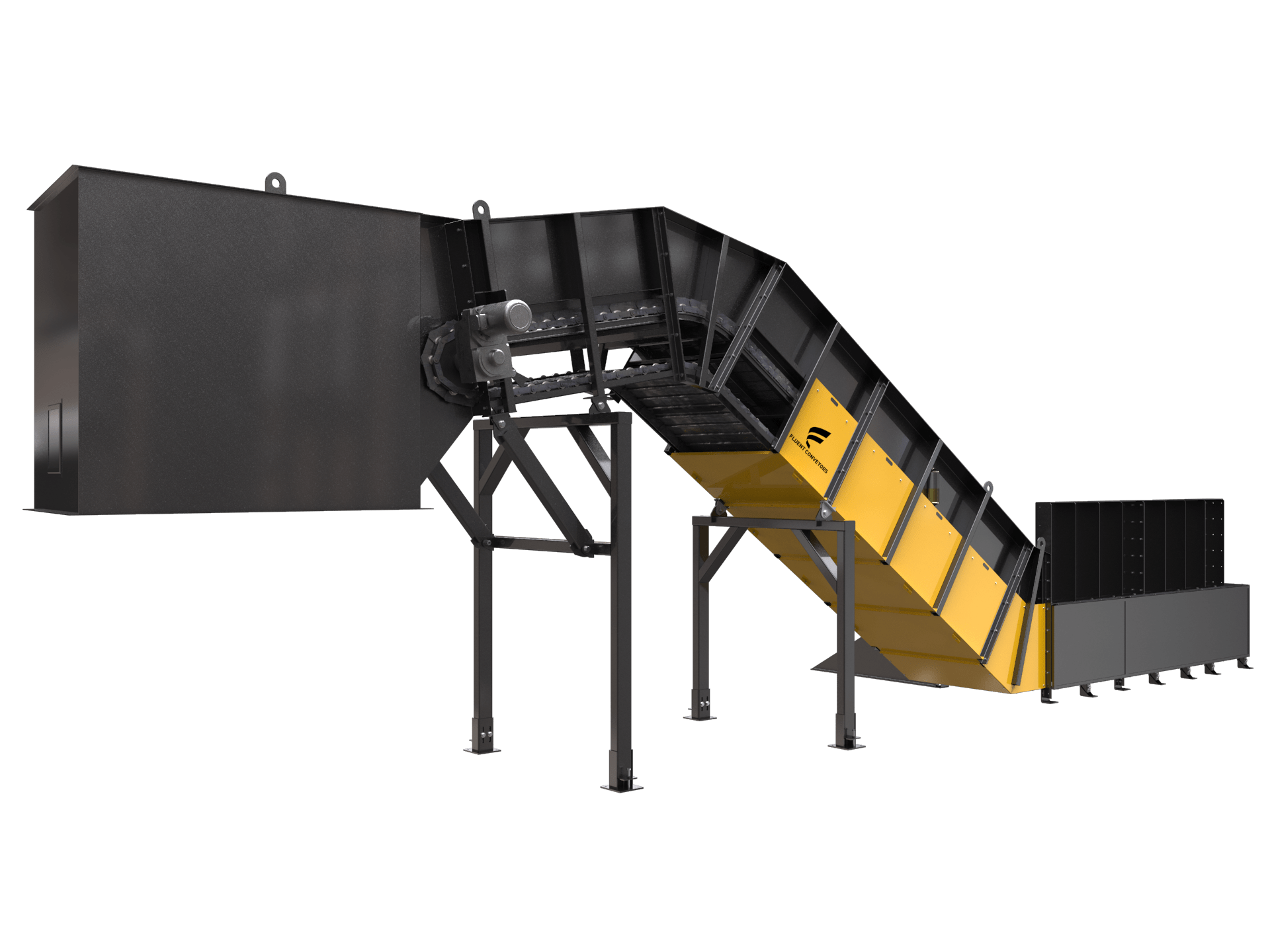
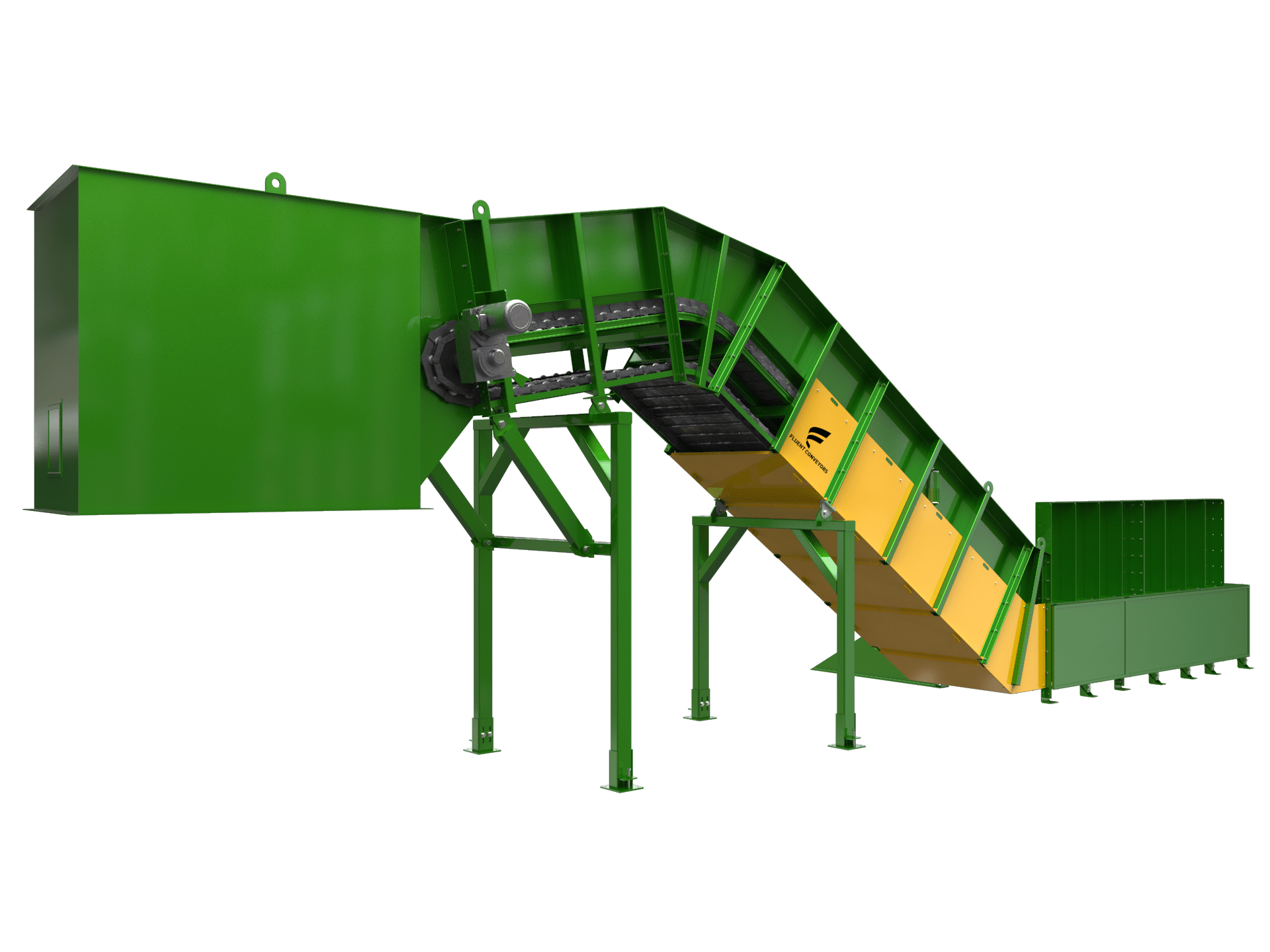
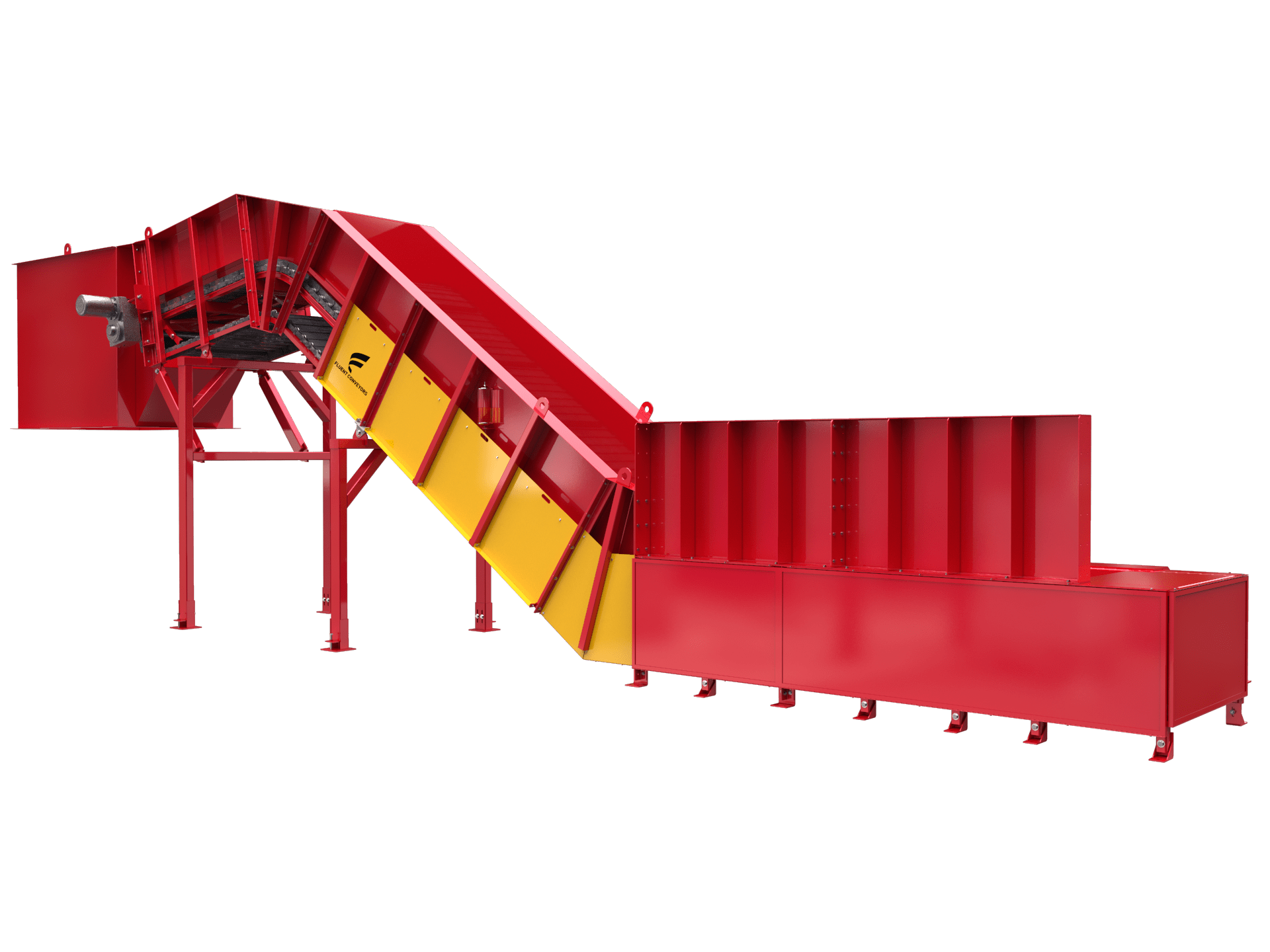
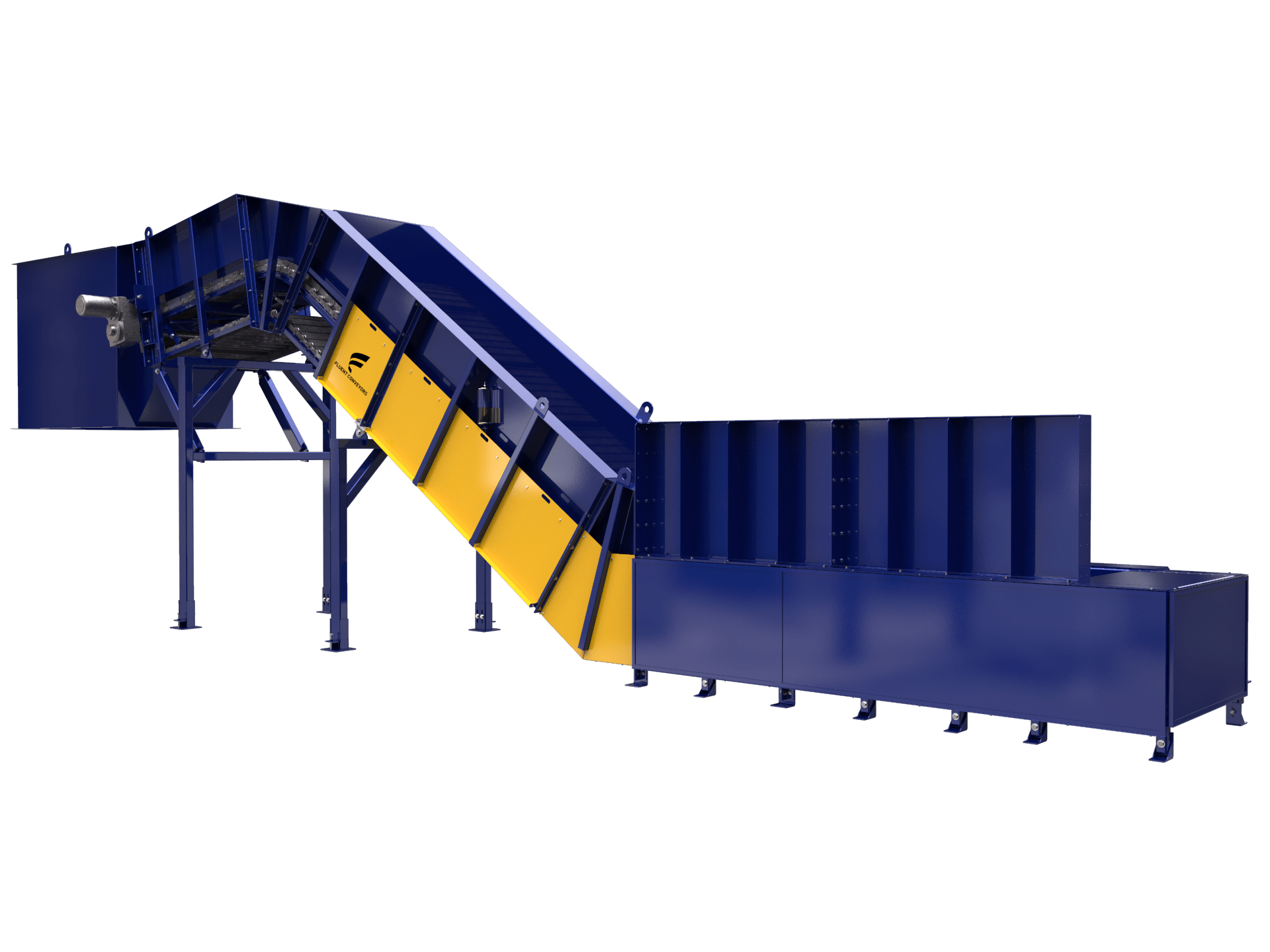
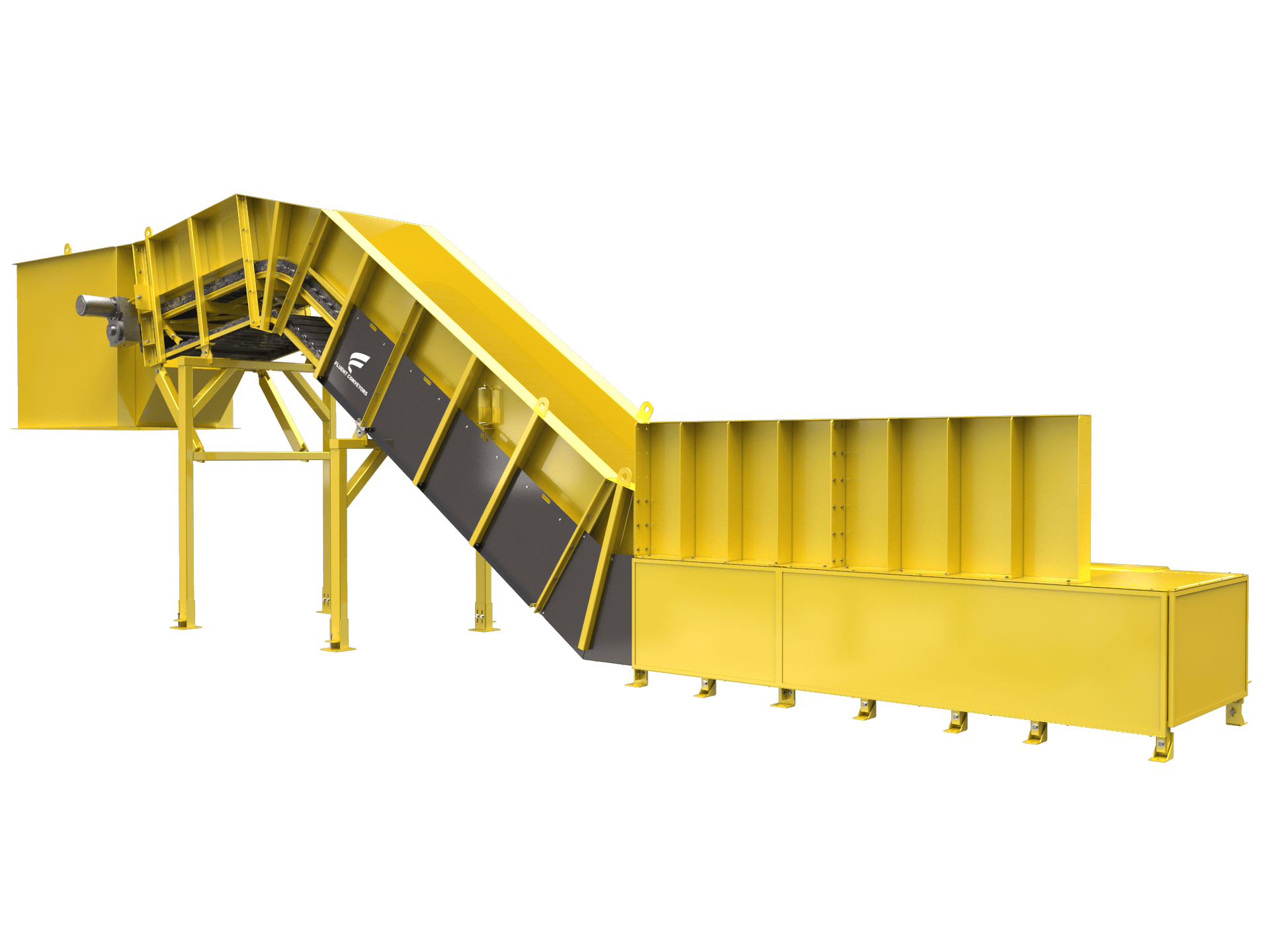
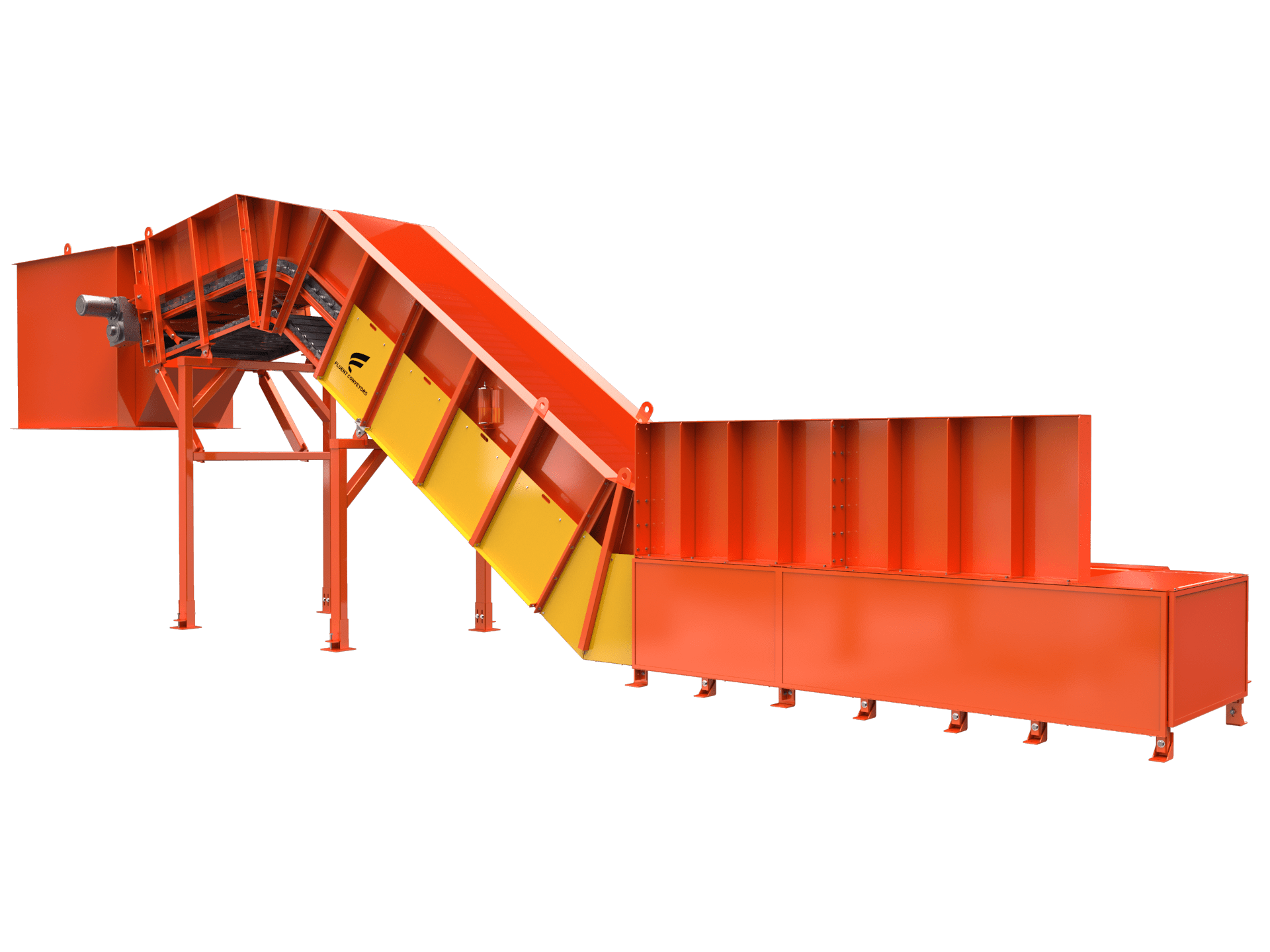
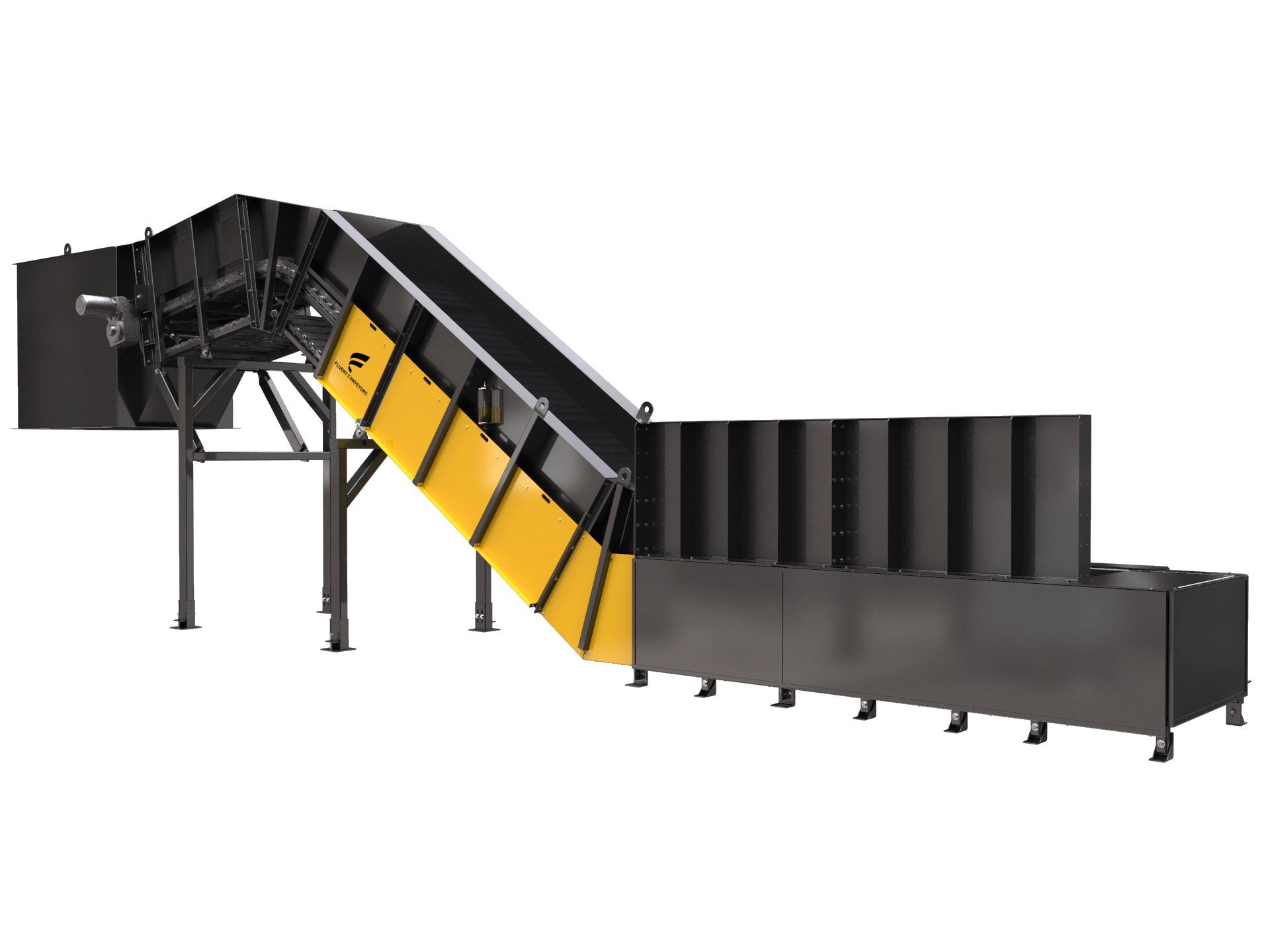
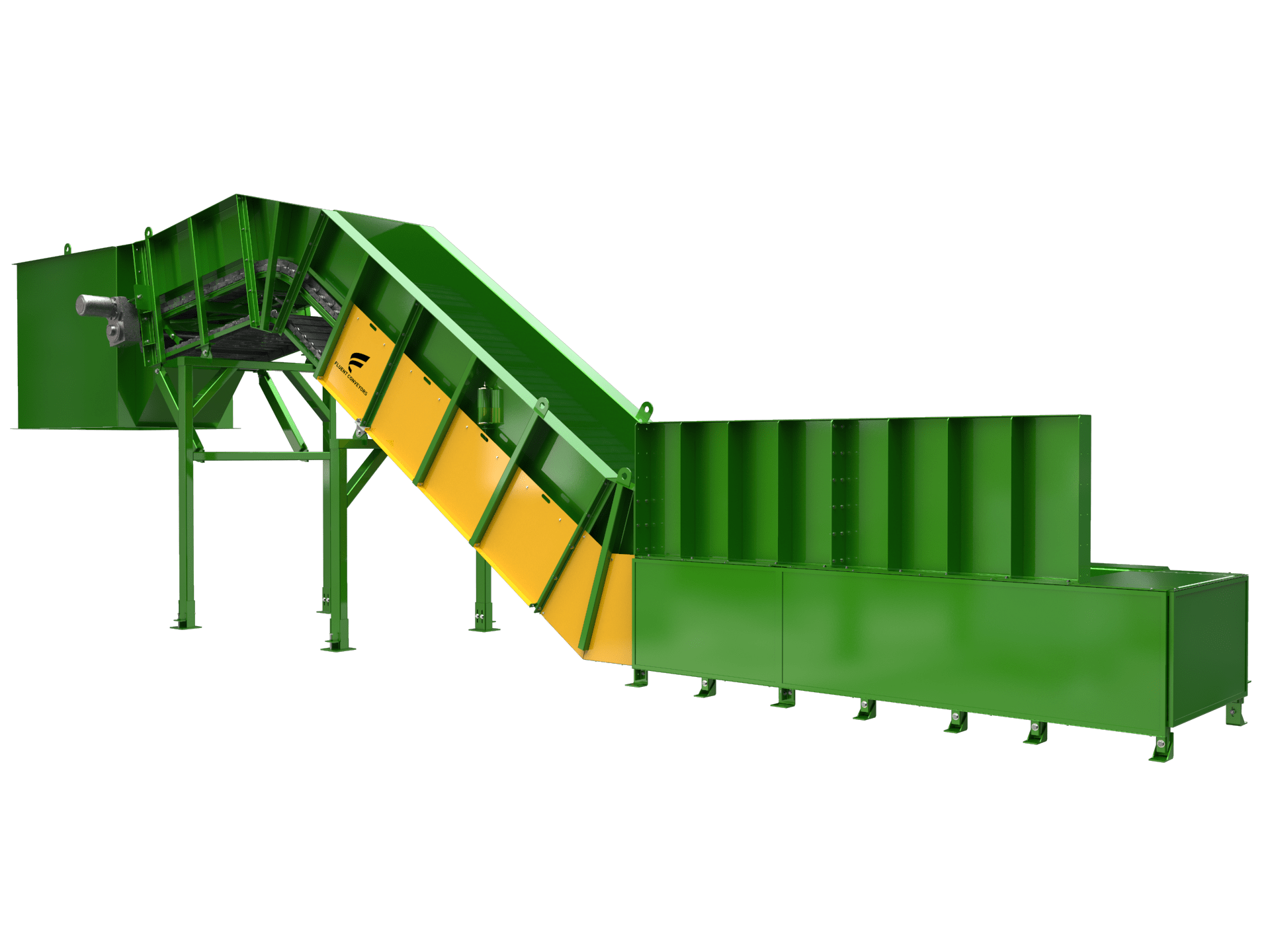
Select Your Color
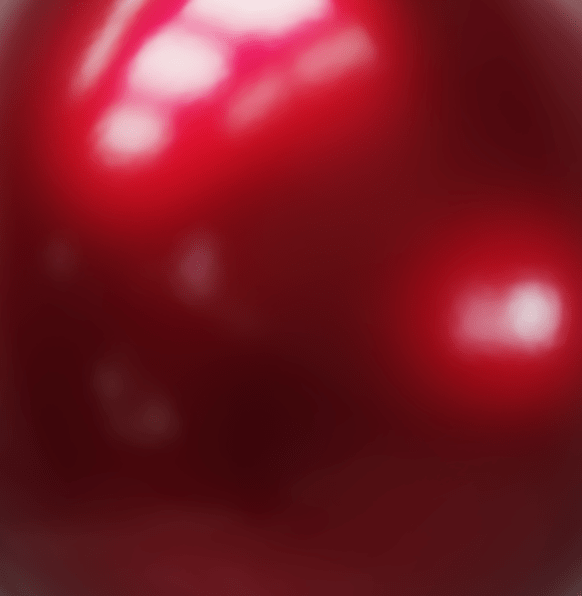
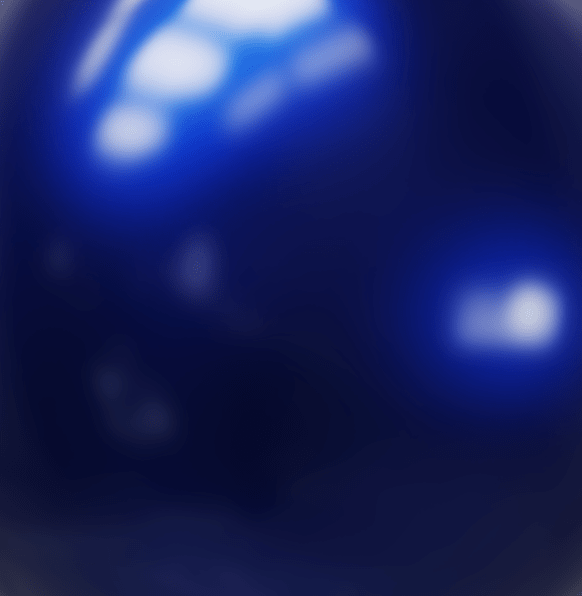
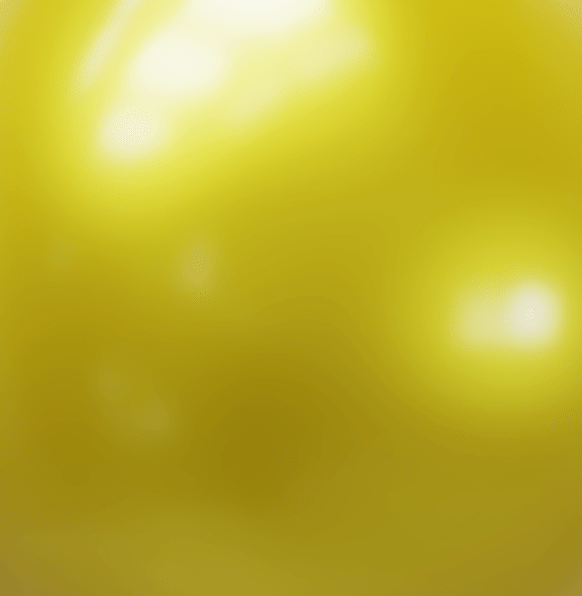
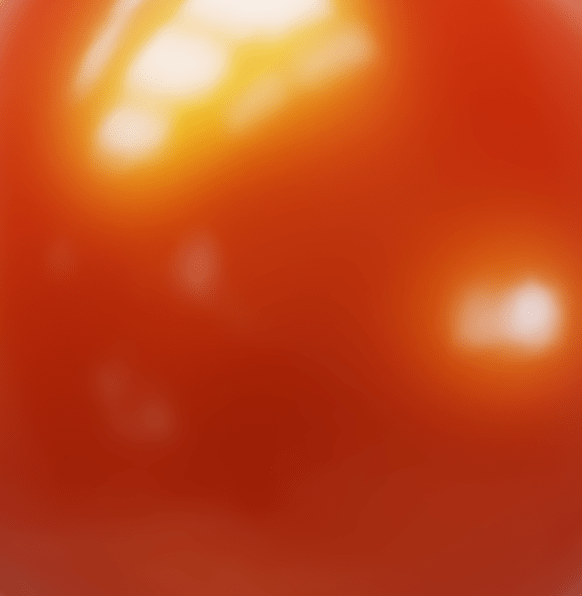
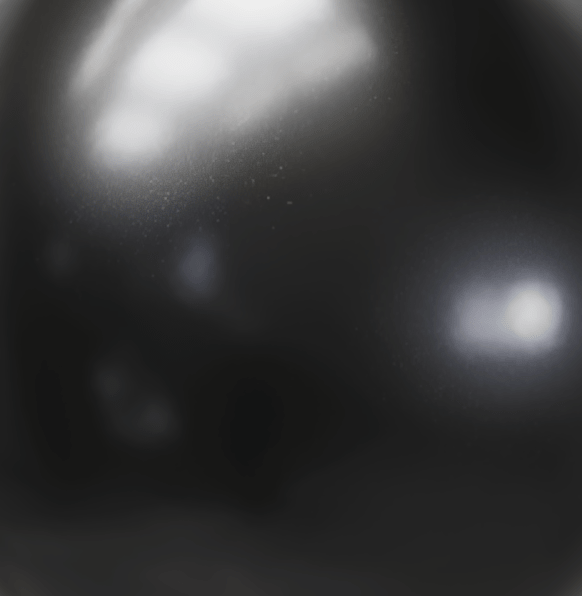
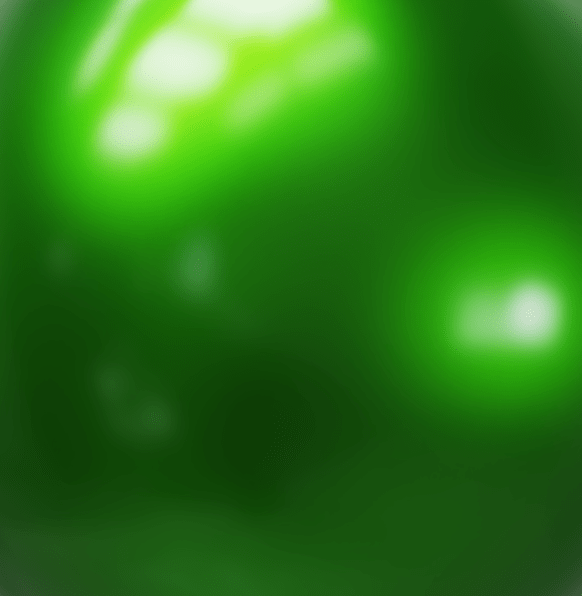
DIRECT SHAFT MOUNTED MOTORS & GEARBOXES:
Fluent Conveyors specs only premium components to complete our equipment and provide a high-quality solution. Fluent Specs Nord Gear Drive units for their quality reputation and exemplary products. Fluent Conveyors can use any specific manufacturer of motors/gearboxes upon request.
COLD ROLLED SHAFTS:
Fluent Shafts are made from cold rolled steel rod and turned to the tightest tolerances in the industry. Every shaft is made custom to fit your specific conveyor.
HEAVY DUTY BEARINGS:
Fluent Conveyors uses bearings that boast cast iron housing, wide inner races providing for larger load capacity than standard duty, B type seals for smooth function and protection against the elements, and the bearings are sized to greatly exceed L10 life hours for the machine load.
FLAME TREATED & HARDENED SPROCKETS:
Fluent Conveyors uses abrasive applications with high shock loading. The inherent strength and flame hardened teeth of these sprockets provide maximum service in the most severe environments. The versatility of flame cut sprockets allows for specialized designs for a variety of customer requirements.
What Customers Are Saying
"In 2018 our company was in a really weird position. We had purchased 2 large expensive conveyors over the last 5 years from 2 different manufacturers (Yes our application is rugged, heavy and has lots of baling wire). Both systems caused non-stop maintenance issues that were becoming very expensive for our company. We were referred to Fluent Conveyors by a local distributor/dealer in our area and from the start, I knew we found the correct manufacturer. Their pre-sales team visited our facility, took the time to listen to our core issues, and allowed our team to become part of the entire design process. I found their team slowing us down to re-validate key dimensions etc to ensure this new system would not only meet our expectations, but help position our capital layout to actually work for us for more than a couple of years. It has been almost 2 years and I can say the Fluent Conveyors team delivered exactly what we expected. No issues, 100% functioning and were are currently exploring adding a brand new system at one of our other facilities in 2020. Thank you for being professional and experts at your craft.
-John & Chris, Virginia
Fluent Conveyors offers 6 inch pitch, 9 inch pitch & 12 inch pitch roller chain belts for our heavy duty roller chain model. Core belt offerings include 220 ply and 330 ply rubber combination belts with c-channel backing, 1/4" thick hinged steel pans with optional c-channel, double beaded apron pans and z pan steel belt conveyors.
All belts offer a wide variety of coped cleats, carbonized & hardened bushings, chain thickness, pan thickness, cleat spacing, hardened sintered steel rollers, 3" & 4" interlocking side wings and much more to meet a wide variety of recycling & waste processing applications.
**Fluent Conveyors offers 100's of custom belt combinations and options. Please contact our sales team for specific requests
Getting Down & Dirty Pit Roller Chain Conveyor
Your instincts are right... You’re looking at the most robust series of conveyors we offer. Top-of-the-line engineering created with the industry’s highest manufacturing tolerances, our advanced RC Series delivers exactly what the market requires.
The Fluent Roller Chain Series is made to play in the big leagues. Fluent Conveyor’s Pit Infeed Roller Chain Belt Conveyors are found in robust applications and best utilized for new and existing pits.
This model delivers exactly what the market requires for high volume rigid and abrasive material as well as high-temperature and other extreme applications. All designs are made to order and customizable. This model requires 3/8-inch-thick or 1⁄2 -inch-thick pit plates and material is typically fed onto the conveyor with a skid steer, bobcat, front-end loader etc. Only the best machinery, transforming your systems and business.
Transfer Roller Chain Belt Conveyor
The Transfer Roller Chain Conveyor ensures smooth operations. It is made to last with easy maintenance, ensuring your system is never lagging.
Fluent Conveyor’s Above Ground Transfer Roller Chain Belt Conveyors are found in robust applications and best utilized to transfer bulk materials spanning long distances and different elevations. This model delivers exactly what the market requires for high volume rigid and abrasive material as well as high-temperature and other extreme applications.
Our conveyors are extremely durable and built for high-performance that stands the test of time. All designs are made to order and customizable. This model is available in inclined, flat, L and S shapes to fit all types of applications. This model primarily used to transfer material from a “feed” conveyor or piece of equipment to another conveyor or piece of equipment.
Uniquely designed to transform your systems into one sleek, seamless operation.
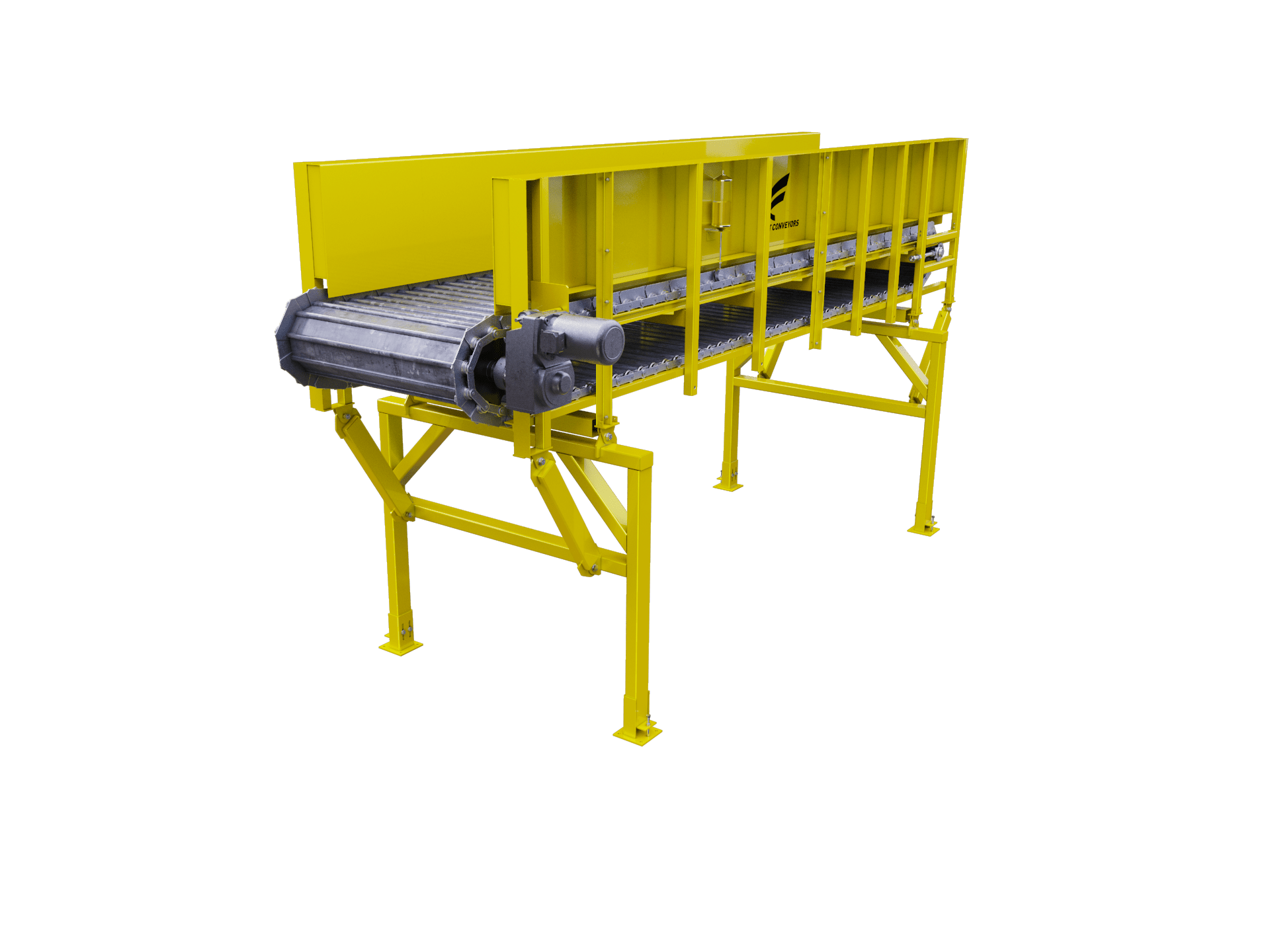
The Above Ground Roller Chain Conveyor
The above ground roller chain conveyor is created to drastically increase productivity and keep your business running at an optimal pace.
This series of conveyors is the most robust series of conveyors we offer. This model delivers exactly what the market requires for high volume rigid and abrasive material as well as high-temperature and other extreme applications. All designs are made to order and customizable. You will always get the perfect machinery for your unique needs.
This model is available in inclined, flat, L and S shapes to fit all types of applications. This model is guarded with expanded metal on the lower horizontal (loading area) to allow for visual inspections of clean-liness and function. Flawless engineering for flawless performance.
Collaborate
At Fluent Conveyors, we look for partners over clients. Your success is our success. Every step along the way, through dynamic collaboration, we ensure high-end experience from pre-sales engineering to install.The process starts with a detailed system design meeting in which fluent sales and engineering staff complete a pre-project kick off call with our customer to gather all necessary info and gain a detailed understanding of their specific needs. The Engineering team designs a unique solution while working with each customer to ensure accuracy and detailed approval drawings. Ensuring your vision comes to life.
Create
Our open creative process ensures you’re always in the driver’s seat. We blend technical expertise with visionary thinking to ensure your expectations are not only met, but surpassed. Fluent Conveyors uses leading edge 3D CAD and automation tools to ensure a process that puts the customer first, provides a speedy turnaround time, error free engagement and a better overall customer experience. End result: engineered product for your specific application type and unique needs delivered in hours – not days or weeks.
Convey
Our processes ensure 100’s of customers across the World precise, efficient, and smooth operations. Each conveyor is tested, validated and approved to verify structural and mechanical operability. It’s just that simple.
FINITE ELEMENT ANALYSIS
We’re here to transform complex problems into simple solutions. Structural analysis gives Fluent Engineers instant access to solve complex engineering problems. These tools give the Fluent Engineering Team the ability to make better, faster design decisions. With the finite element analysis (FEA) tools the Fluent Engineering Team can customize and automate solutions for your unique application and parameterize them to analyze multiple design scenarios. Optimizing your systems to level up your performance.
STRENGTH ANALYSIS
Upgrading to the highest-grade machinery means giving your business the strongest systems possible. The strength of components is a key requirement in understanding a product’s performance, lifecycle and possible failure modes. Max conveyor loads, thermal stress, bolt tension, pressure conditions, belt chain pull, and rotational acceleration are just some of the factors that will dictate strength requirements for materials and designs. Fluent Conveyors Engineering Team leverages software to predict the strength required for maximum stresses under full loads. We only give you the strongest machinery to make sure you never have to stress about its performance.
REAL-LIFE IMPACT ANALYSIS
Our Fluent Conveyors Engineering Team designs for real-life impact. We use cutting edge impact analysis testing to calculate the forces between the material being conveyed and the conveyor as well as the resultant deformation or damage. Ensuring each conveyor is designed from the ground up to handle the real-life stresses for specific materials and applications. Engineered with grit for years of impact.
DURABILITY & ENDURANCE
Designed to endure the test of time and position you as the King of longevity. Fluent Conveyors aligns all engineering processes to ensure all manufactured conveyors are tested for durability. Building durable products is one of the main focuses of Fluent Conveyors. Fluent designs each machine to reduce warranty costs and increasing reliability. Fluent uses our modeling software to understand how designs will behave over time as load cycles increase to avoid unexpected failures and warranty costs. We plan for all the worst case scenarios, so you don’t have to worry about them.
Fluent Conveyors is 100% focused on customer safety for all their equipment. This is one of the most important parts of our process. If your team has any internal safety requirements for existing equipment we want to ensure we design our systems to match or exceed those requirements.
We do not authorize removing safety guarding, conveyor safety switches, cords, controls etc. You must consult your local dealer or our engineering department to adjust anything regarding our equipment. If not followed, your warranty becomes void at that time.
Safety offerings include: dead man plates, e-stop / pull cords, protective guarding, manuals etc.
Please Note: The Fluent Conveyors Roller Chain model is extremely powerful and can cause great harm. All maintenance must be performed by a trained and authorized employee or dealer. Before performing any service please lock out / tag out ("Do Not Operate") the electrical inputs to our equipment.
Review CEMA or OSHA to review current safety requirements for conveyors and related equipment.
Fluent Conveyors offers complete and customized heavy duty discharge and transition hoppers for both new and existing pieces of equipment. Our discharge hoppers (provided with the correct CAD (DXF, DWG, STP, IGES) files)) seamlessly meet the bolt holes on all horizontal baler manufacturers including: American Baler, Harris Baler, International Baler, G- Baler, Harmony, Balemaster, Maren, Enterprise, Bollegraf and more!
The Fluent Engineering team is also well versed in working directly with other OEM equipment: shredders, conveyors, trommels, sort systems, hammermills and more. Key manufactures include SSI Shredding, Hustler Conveyors, Vecoplan, Karl Schmidt, Untha and more!
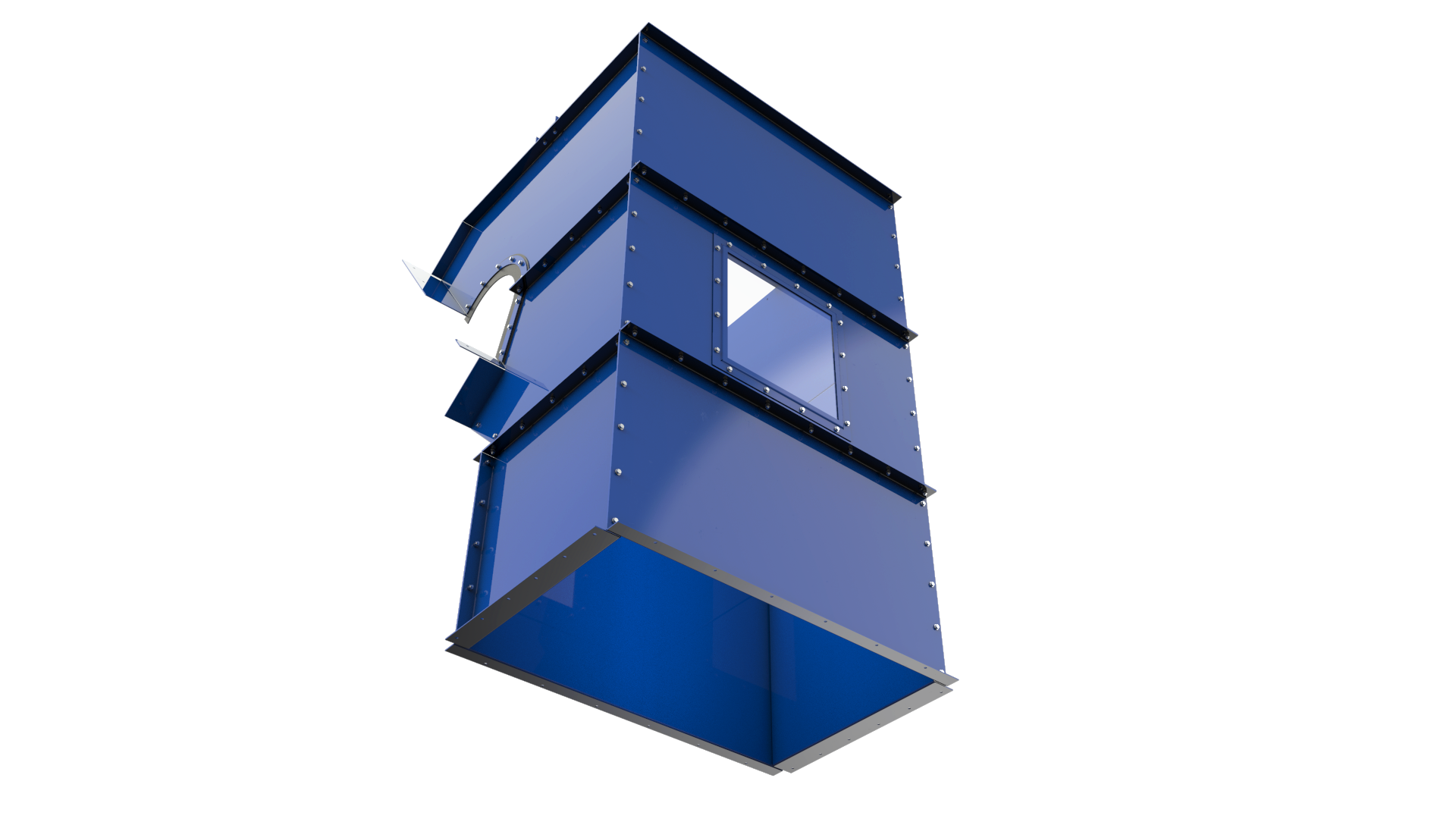
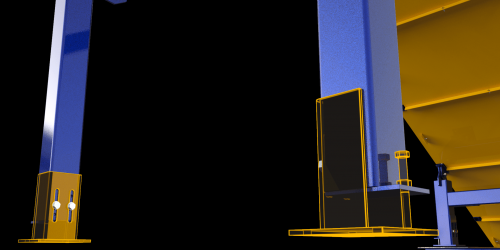
Delivered with everything you need for seamless installation. Fluent Conveyors provides each conveyor with supports that can adjust + - 1.75” on the above grade supports. These come standard with jacking bolts to allow for easier leveling and install. Giving you a seamless experience.
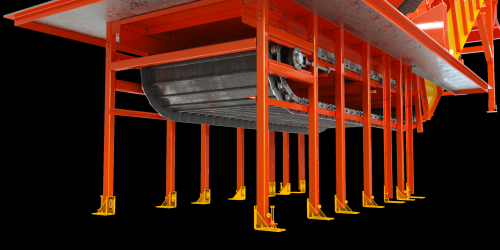
Precise installation for a level foundation. Fluent Conveyors. Provides each pit section with +/- 1” Adjustable Foot Pads with jacking bolts spread evenly throughout to allow for easier leveling and install. So you can get moving faster.
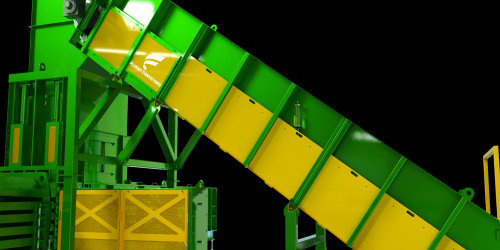
Robust components to take on the heavy lifting. Fluent Conveyors supplies our conveyors with supports and knee braces that are clevis mount using 3/8” and ½” thick plate steel. These connections are designed to be robust and simplify install. Making your job as simple as possible.
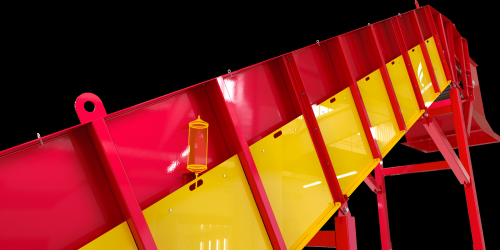
Simplifying long term maintenance for systems that outlast the rest. Fluent Conveyors supplies solenoid driven auto oilers paired with a nylon brush wheels to ensure even and consistent oil distribution on the rollers and chain. This is to simplify maintenance and increase the life of the machine up to 30X longer. Top-of-the-line performance built to stay ahead of the rest.
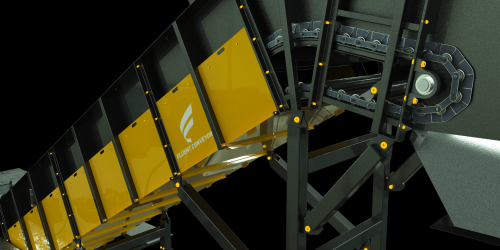
Top grade hardware you can trust. Fluent Conveyors uses only grade 8 hardware for all load bearing and mechanical connections. This hardware is hardened and plated to provide a more robust and extreme element resistant solution.
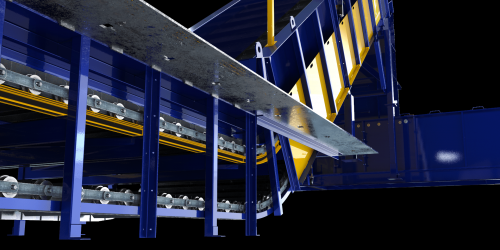
Load bearing guides for seamless performance. Fluent Conveyors roller chain conveyors use custom rolled and formed 25lb - 35lb rail for our carrying track.
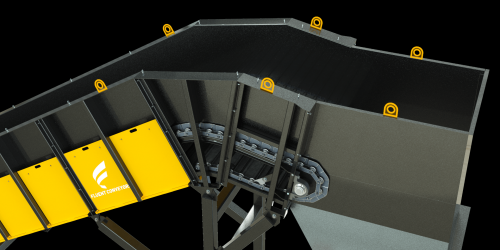
Strategic engineering for simplified maneuvering and installation. Fluent Conveyors provides all equipment with strategically located ½” thick plate steel lifting lugs to simplify rigging and install.
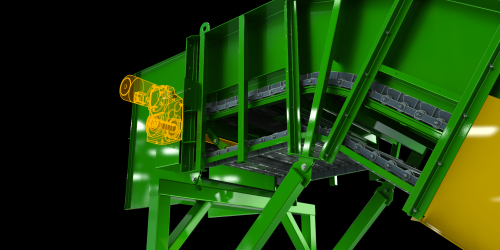
Smooth drive guaranteed. Fluent Conveyors Specs Nord Gear drives and motors to provide a premium quality drive unit. *Other drive unit manufacturers can be supplied upon request.
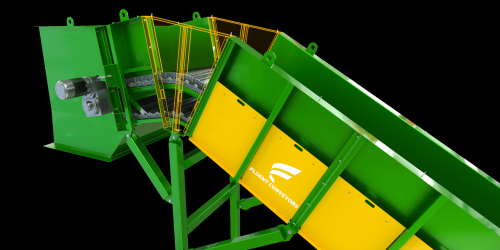
Custom tailored to maximize your throughput. Fluent Conveyors custom designs each machine to the customer needs. We can provide incline and nose over angles from 0 to 45 deg. All nose over angles have 25lb - 35lb carrying rail.
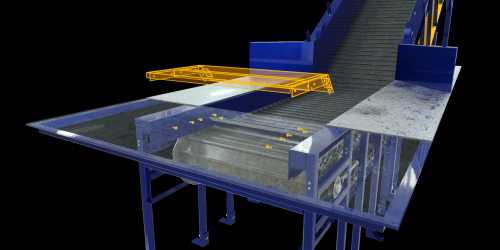
Easy access for effortless maintenance. Fluent Conveyors RC series machines are designed with robust removable tail covers (10 bolts) to provide easy access for belt removal/replacement.
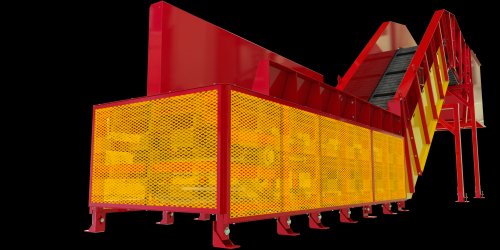
Fluent Conveyors provides all above ground RC series conveyors with expanded metal guarding on the lower horizontal to keep your employees safe.
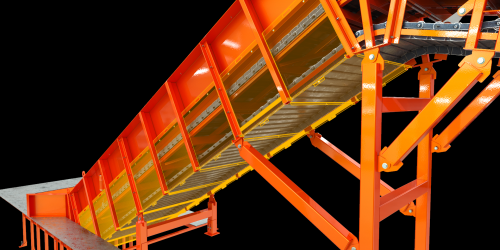
Ensuring your team stays safe on the job. Fluent Conveyors provides 10 gauge formed sheet safety guarding up to 8’ above the floor standard. It is optional to have a fully guarded conveyor or use expanded metal guards.
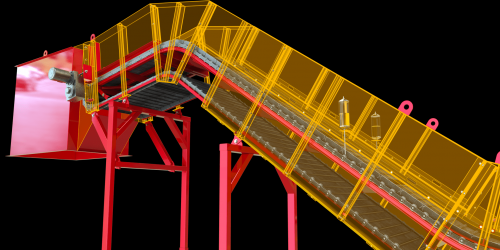
Designed to optimize endurance for years of heavy lifting. Fluent Conveyors builds the RC series machines using ASTM A-36 Steel 3/16” wall structural tubing and ¼” thick formed steel plates with 25 lb rail and precisely positioned gussets.
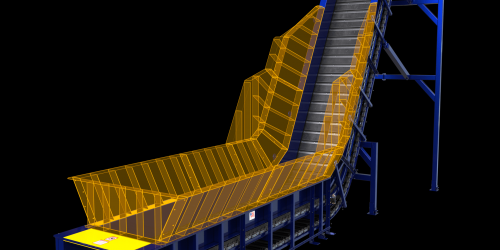
Metering Hopper is all about quality and durability. We've built our product with care and we've made sure that our customer would be satisfied with it. Metering Hopper is a high-quality, long-lasting product that will last for years. It's also sealed with marine grade paint to ensure a long life outside.
Detailed & Customized Mechanical Engineering
FLUENT CONVEYOR DESIGN GUIDELINES
Fluent Conveyors Roller Chain Series Conveyors are designed with cutting edge software to be ahead of the curve. Giving you an edge above the rest. All machinery is validated using premium 3D CAD software and manufactured to industry leading tolerances and standards. After completion of a design, the engineering team releases to quality assurance, allowing secondary engineers to validate critical dimensions, calculations and manufacturability. After initial and secondary engineering approvals, projects are released to purchasing and the manufacturing facility by the lead manufacturing engineer. Our experts only approve the highest caliber work to ensure you’re working with nothing but the best.
FLUENT CONVEYOR MANUFACTURING GUIDELINES
Fluent Conveyors Roller Chain Series conveyors are made in innovative facilities to equip you to level up your business. With all the industry leading equipment and processes, Fluent Conveyors production team has over 100 years of combined experience paired with a facility of more than 85,000 square feet. The core facility has a paint booth, 40,000 square feet of dedicated assembly, 6 – welding stations, CNC fabrication equipment, 10 – overhead cranes and more. Parts are cut/machined on CNC Routed machines and bent on CNC Brakes for the best in industry tolerances. Every weld is tacked and re-measured for accuracy then completed by the staff of certified welders. Once manufactured, every conveyor passes through a 3-step finishing process starting with sandblasting and ending with high grade paint. Ensuring you’re working with smart, flawless machinery.
CONVEYOR TESTING OVERVIEW
All conveyors are delivered to you ready for work. Assembled and released to a detailed quality assurance checklist to make sure your machinery can hit the ground running. This includes key validations such as; weld examination, sub-assembly QC, 10 hours of tested run time, head shaft height validation, frame levelness, frame width validation, overall height/length, belt speed, belt tracking, belt and conveyor alignment, electrical requirements, incline and nose over angle verification and all other major specifications. Making sure your machinery is set up for long term success.
SHIPPING OVERVIEW
We ship the smartest way possible, to make your job easy. Fluent Conveyors Product shipments are carefully planned in CAD software to be loaded in an organized, space saving, and safe manner ensuring that all products arrive on-site the same as when they left our facility. Loose items are boxed and marked, assembled parts and components tightened to endure the rigors of freight and shipping. We’re here to make sure every step of the process is seamless.
- In Pit (New or Old)
- Above Ground
- Nose Over (Flat, Angled Down)
- Transfer
- Reversing
- ASTM A-36 Steel
- 3/16” Wall Thickness Square and Rectangular Tubing
- 25lb Rail on Carrying Track
- 1/4” Formed Sheet Metal
- Standard Removable Tail Cover
- 10 Gauge Gusset Plates
- Load Depth from 12” to 60”
- AC or DC Electric Automatic Drip Feed Oiler with Brush
- ASTM A-36 Steel
- 6” Square 1⁄4” Thick Tube Boxed Supports
- Clevis Mount Supports & Knee Braces for Ease of Install & Alignment
- +- 1.75” Adjustable Incline Supports
- +-1” Adjustable Pit Section Supports
- Custom Loading Hoppers Available
- Formed ASTM A-36 10 Gauge – 1⁄4” Thick Steel .
- Made for Skid Steer Loading, Cart Tipper, Push On, Hand Loading
- Custom Discharge Hoppers Available.
- Formed 10 GA Steel
- Angle Iron Frame
- Custom Fit Per Specs (CAD drawings required)
- To Be Used With All Roller Chain Belt Models (Rubber Combo, Hinged Steel, Apron Pan & Z Pan)
- Single Feed Automated Lubricator with 1/2" NPT
- 1 Gallon Acrylic Reservoir With Lightweight & Durable Polypropylene End-plates
- Electrical Requirements 120 Volts @ 60 Hz
- Shank Brush 3" Diameter x 1" Wide Roto Nylon
Oil Recommendations Are Based On Environmental Conditions
- 3/8” or 1⁄2” Thick Pit Plates
- Optional Pit Plate Wings
- Optional Removable Pit Plates with Chain Mount and Key / Key Stock
- Custom Options Per Customer Requirements
- Side Guard and Bottom Guard to 8’ Above Grade
- Full Conveyor Guarding is Available
- Above Ground Option Includes Full Lower Horizontal Guarding
- 1⁄2” Thick Plate (Welded)
- 2-1⁄2” Dia. Eyelets For Easy Unloading/Loading/Installation
- 48” to 96” widths available (Additional Options Up To 120" Wide)
- 4", 6", 9" Pitch Chains Available (12" Available On Select Belts)
- 3”, 4” and 5” Rollers Available
- 9,000lbs to 25,000lbs Chain Pull Available
- Rubber Combo Belts with 2Ply 220 and 3Ply 330 (84” width max standard width)
- Hinged Steel Belts 3/16” and 1⁄4” Pan Thickness
- Apron Pan Belts 3/16”, 1⁄4”, 3/8”, 1⁄2” Pan Thickness
- Z-Pan Belts 3/16”, 1⁄4”, 3/8”, 1⁄2” Pan Thickness
- 5.0 HP – 25 HP Shaft Mounted Drives
- *Std. High Efficiency Motors
- *Optional Ultra High Efficiency/Wash Down/Corrosion Resistant
- *230-460V 60Hz
- *575V 60Hz, 208V 60 Hz, 400V 50 Hz,115-230V 60 Hz (1 phase) (10245, image Motor)
- Optional Sealed Guarding To Protect Against Outdoor Environments
- Standard E-Stops
- E- Stop Pull Cords
- Dead Man Plate
- Safety Halo
- Personal Safety System
- Motor Overload
- Standard Roll Back Guards
- Outdoor Rated Electronics (NEMA 4)
- Integrated to Baler Controls
- Optional VFD (Variable Frequency Drives)
- Optional Custom Control Panel
- Remote IOS/Android Controls
- Optional Motor Brake with Reversing Conveyor
- We Will Work With Any OEM To Meet The Integration Requirements
- Back Side Push Wall
- Pushing Ramps
- Solid Lower Horizontal Decking
- Mezzanine Structures
- Maintenance Walkways
- Lower Horizontal Guarding
- Fully Enclosed, Dust Removal System Flanges
- Rail Guards
- Feed Hopper
- Variable Speed Drive
- Photo Eyes
- Belt Brush/Wiper
- Custom Load Depth
- Standard Fluent Gunmetal Grey
- Harris Baler Blue
- American Baler Blue (RAL 5010)
- SSI Black
- International Baler Blue (RAL 5010)
- Color Match with RAL Available Upon Request
3-7 Plastic, Aluminum, Bagasse, Bio-Waste, Bulk Materials, C&D, Card-Stock, Coal, Concrete, E-Waste, Ferrous, Foam, Foundry, Glass, Hay, HDPE, Iron Ore, LDPE, Medical Waste, Mixed Paper, MSW, Non-Ferrous, Cardboard (OCC), Old Newspaper (ONP), Other, Paperboard, PET, Rubber, Refuge, Sheared Scrap, Single Stream, Stone, Stover, Textiles, Tires, Tissue Paper, Wood Products
As well as producing bespoke conveyor systems, we also supply custom replacement belts and parts to ensure no client sees their assembly line stay offline for an extended period of time. From replacement motors to sprockets, everything is covered if a client comes across a failing element of their conveyor system.
Sadly, it’s inevitable your clients will face some type of issue with their conveyor system at some point. Even with Fluent Conveyors’ best equipment in place, conveyors are going to suffer from wear and tear due to their demanding nature. However, being able to offer a solution at any time will be appreciated by your clients.
Are You Ready To Schedule Some Time With The Fluent Conveyors Team? Great!
Our Process Is Typically Very Lean & Detailed! We Prefer Not To Waste Our Customers Time! Engineering Time & Revisions Takes A Considerable Amount of Time For Both Customers & Our Engineering Team.
Please Contact Us If the Roller Chain Conveyor Specifications Match What You Need & You Are Comfortable With:
- Price Can Range From $40,000 - $300,000+ Per Conveyor
- Lead Time of 10 – 12 Weeks (From Down Payment & Signed Approval Drawings)
- Pre-Payment on Engineering Time if The Project is Complex
- 50% Down-Payment, 40% 2 Weeks Prior To Ship, 10% Net 30 Upon Install
-
What makes this roller chain belt heavy duty?
Fluent Conveyors designs these machines specifically for the toughest and most abusive environments. We understand that the real world isn’t clean and it’s not always practical to load heavy materials with little impact. Fluent Conveyors builds the Roller Chain series conveyors and belts out of thick-walled structural steel and formed steel plate. Our engineering department reviews all critical loads and impact zones for each application to ensure the direct forces to the loading zones and belt chain pull have a factor of safety of 1.3 above the application requirements.
We leverage 25-pound rail, ¼" and 3/16” thick formed steel plate throughout the core design with strategically placed gussets, cross members and impact rails to withstand vibrations and impact forces.
-
Can this conveyor model be configured with different belt options?
The roller chain conveyor series is a made to order conveyor. We can leverage existing projects to help reduce lead times for your application but if you have space constraints or an existing pit, we can customize the design to seamlessly match your facility.
On the pre-sales side we get as much data and information on each application to correctly size chain, sprockets, bushing, pins, rollers, belt pans (rubber, hinged steel, apron pan or z pan) etc. as well as making sure the surface of the roller chain belt has the correct strength and load capacity to exceed your application requirements.
-
What type of motor / drive unit is used for this model?
Fluent specs parallel shaft gear reducers and IP55 integral (direct mount) motors. These are standard with 230/460V at 60Hz. Fluent can change this to match your specific requirements whether it be helical bevel gears, a certain manufacturer for continuity or a different power input.
-
What is a roller conveyor system?
Roller conveyor systems can be powered by a motor and drive system or through gravity. These conveyors consist of a series of roller that are closely spaces to each other to distribute the load.
Gravity roller conveyors can be level or declined. The level gravity roller conveyors are used for accumulation and the product can be pushed by hand. The declined conveyors use gravity to move the conveyed product down the slope. These can be very cost-effective solutions for moving boxes and pallets throughout a distribution facility.
Powered roller conveyors use either a series of bands or belts, or gears and chains to turn some or all the rollers. These are called the live rollers. These conveyors can have different segments that are powered separately from each other allowing for accumulation and powered flow. This type of conveyor is extremely flexible in its design and capabilities. Powered roller conveyors are commonly found in locations where there are complex needs for the movement of the conveyed materials.
-
When do you replace a drive chain in a conveyor belt?
Similarly, to your car, conveyor drive systems need regular maintenance and upkeep to run smoothly for a long time.
One of the main indicators of a worn chain is the wear elongation. If the chain has elongated more than 3% from its original pitch length, then it is necessary to replace the chain. This length can be determined by measuring from one chain pin to the next in a taught part of the chain (a slack segment of chain will not give accurate measurements). Using multiple pitches will increase the accuracy of your measurement. Look up the ANSI standard pitch for your chain (it may be stamped on the side bars) and compare. Chain wear scales are extremely helpful for this measurement.
A tell-tale sign that a chain is worn and elongated is that the chain will be riding high (or up near the tip of the sprocket teeth) on your largest sprockets in the system. If you see this replace your chain immediately.
If your chain is visibly damaged, bent or rusty it is recommended that you replace it immediately.
-
What makes this roller chain belt heavy duty?
Fluent Conveyors designs these machines specifically for the toughest and most abusive environments. We understand that the real world isn’t clean and it’s not always practical to load heavy materials with little impact. Fluent Conveyors builds the Roller Chain series conveyors and belts out of thick-walled structural steel and formed steel plates. Our engineering department reviews all critical loads and impact zones for each application to ensure the direct forces to the loading zones and belt chain pull have a factor of safety of 1.3 above the application requirements.
We leverage 25-pound rail, ¼" and 3/16” thick formed steel plate throughout the core design with strategically placed gussets, cross members and impact rails to withstand vibrations and impact forces.
-
Can this conveyor model be configured with different belt options?
The roller chain conveyor series is a made to order conveyor. We can leverage existing projects to help reduce lead times for your application, but if you have space constraints or an existing pit, we can customize the design to seamlessly match your facility.
On the pre-sales side we get as much data and information on each application to correctly size chain, sprockets, bushing, pins, rollers, belt pans (rubber, hinged steel, apron pan or z pan) etc. as well as to make sure the surface of the roller chain belt has the correct strength and load capacity to exceed your application requirements.
-
What type of motor / drive unit is used for this model?
Fluent specs parallel shaft gear reducers and IP55 integral (direct mount) motors. These are standard with 230/460V at 60Hz. Fluent can change this to match your specific requirements whether it be helical bevel gears, a certain manufacturer for continuity or a different power input.
-
What is a roller conveyor system?
Roller conveyor systems can be powered by a motor and drive system or through gravity. These conveyors consist of a series of rollers that are closely spaced to each other to distribute the load.
Gravity roller conveyors can be level or declined. The level gravity roller conveyors are used for accumulation and the product can be pushed by hand. The declined conveyors use gravity to move the conveyed product down the slope. These can be very cost-effective solutions for moving boxes and pallets throughout a distribution facility.
Powered roller conveyors use either a series of bands or belts, or gears and chains to turn some or all the rollers. These are called the live rollers. These conveyors can have different segments that are powered separately from each other allowing for accumulation and powered flow. This type of conveyor is extremely flexible in its design and capabilities. Powered roller conveyors are commonly found in locations where there are complex needs for the movement of the conveyed materials.
-
When do you replace a drive chain in a conveyor belt?
Similarly to your car, conveyor drive systems need regular maintenance and upkeep to run smoothly for a long time.
One of the main indicators of a worn chain is the wear elongation. If the chain has elongated more than 3% from its original pitch length, then it is necessary to replace the chain. This length can be determined by measuring from one chain pin to the next in a taut part of the chain (a slack segment of chain will not give accurate measurements). Using multiple pitches will increase the accuracy of your measurement. Look up the ANSI standard pitch for your chain (it may be stamped on the side bars) and compare. Chain wear scales are extremely helpful for this measurement.
A tell-tale sign that a chain is worn and elongated is that the chain will be riding high (or up near the tip of the sprocket teeth) on your largest sprockets in the system. If you see this, replace your chain immediately.
If your chain is visibly damaged, bent or rusty it is recommended that you replace it immediately.